When you're in the market for a fiber laser cutting machine, you'll likely reach out to multiple suppliers and receive various quotes. These quotes will often list different laser sources—such as IPG, nLIGHT, MAX, and Raycus. Understanding the differences between these laser sources is crucial for selecting the most suitable option for your needs. If you need to cut materials like aluminum, copper, or brass, it's advisable to consider an IPG Laser Cutting Machine. IPG laser sources are renowned for their efficiency and reliability, but for cutting high-reflective materials specifically, the nLIGHT laser source is highly recommended. nLIGHT holds patents for cutting such materials, which helps protect both the laser source and cutting head from potential damage. This guide will intoduce the IPG laser cutting machine and help you navigate the options and choose the right machine.
Comparison Between IPG, Raycus and Max.
- Country: Raycus and MAX are all Chinese brand, while IPG is German brand.
- Cutting ability:the same laser power for the same materials, their cutting ability are same.
- Raycus:Best brand in China, but the delivery time will be longer because of the virus;
- Chinese famous brand, cost-effective.Max is also good , Max is located in Shenzhen, they are yonger than Raycus, but now their market occupation is increasing.Especially, during this virus period,
- The advantages of IPG laser source.
- 1)High photoelectric conversion rate.It can reach 45%, other brands are only about 25%,so it can save more cost for you;
2)German brand, good quality, laser power weakened slower than other brand;
3)High market share, a certain degree of reaction to brand strength and quality;
4)low failure rate, only 3%;
5)light power can be seen in real time;
6)after-sale service spots all over the world, problems can be resloved in time;
Our suggestion:It depends on the client’s budget and cutting demands.If client has enough budget, we recommend to choose IPG.If not, Max will be a better choice.
If you have any other questions,pls feel free to contact Krrass sales team for help.
What Is IPG Laser Cutting Machine
The IPG Laser Cutting Machine is a state-of-the-art device designed for precision metal cutting using fiber laser technology developed by IPG Photonics, a leading innovator in the laser industry. These machines utilize high-powered laser beams to cut through various materials with remarkable accuracy and speed. IPG's fiber lasers are known for their efficiency, longevity, and ability to produce high-quality cuts, making them a preferred choice in industrial applications.
In the competitive landscape of laser cutting technology, IPG Laser Cutting Machines stand out for their superior performance and technological advancements. Their importance is underscored by their widespread use in diverse sectors such as automotive, aerospace, and metal fabrication, where precision and reliability are critical. The ability to handle a broad range of materials and thicknesses while maintaining high cut quality makes IPG lasers essential for modern manufacturing processes.
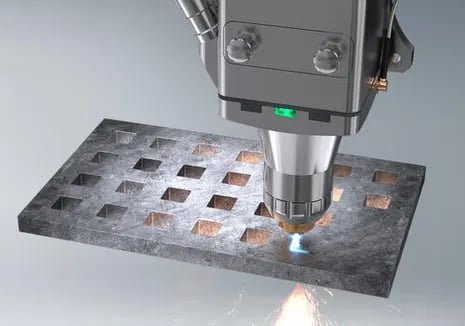
Applications of IPG Laser Cutting Machine
1. Automotive Industry
- Component Fabrication: IPG Laser Cutting Machines are used to cut complex components such as chassis parts, body panels, and exhaust systems. Their precision ensures that parts meet strict quality and safety standards.
- Customization: For high-end and custom vehicles, these machines provide the flexibility needed to produce intricate designs and personalized features.
2. Aerospace Industry
- Structural Parts: The aerospace sector relies on IPG lasers for cutting lightweight, high-strength materials like aluminum and titanium. These lasers help create critical structural components with high accuracy.
- Engine Components: Precision cutting is essential for manufacturing intricate parts of jet engines and other aerospace systems, where even the slightest deviation can impact performance.
3. Metal Fabrication
- Sheet Metal Processing: IPG lasers efficiently cut through sheet metal of various thicknesses, making them ideal for producing parts for machinery, equipment, and enclosures.
- Prototyping and Production: Whether for creating prototypes or high-volume production runs, these machines offer the precision and speed needed for effective metalworking.
4. Electronics Industry
- Circuit Boards: In electronics, IPG Laser Cutting Machines are used for cutting and engraving printed circuit boards (PCBs), enabling the production of detailed electronic components.
- Enclosures and Components: The ability to cut fine details and small parts makes IPG lasers suitable for producing enclosures and components for electronic devices.
5. Industrial Equipment
- Custom Machinery Parts: IPG lasers are employed to cut and shape parts for industrial machinery and equipment, ensuring they meet precise specifications for optimal performance.
- Tooling and Dies: The ability to create high-precision tooling and dies helps in manufacturing various industrial tools and components.
6. Architecture and Construction
- Decorative Elements: IPG Laser Cutting Machines are used to create intricate decorative elements for architectural projects, such as facades, screens, and custom metalwork.
- Structural Components: The precision cutting capabilities are also utilized for structural elements in construction, including beams, columns, and brackets.
7. Artistic and Signage Applications
- Custom Signs: The versatility of IPG lasers allows for the creation of custom signs and graphics with detailed designs and clean edges.
- Artistic Projects: Artists use IPG lasers to cut and engrave metal, wood, and acrylic for unique and personalized art pieces.
IPG Laser Cutting: From Invention to Innovation
In 1990, lifelong laser pioneer Dr. Valentin Gapontsev proposed the world's first high-power fiber laser design which used laser diodes to pump along the length of a doped optical fiber. Shortly after, Dr. Gapontsev developed the first five watt fiber laser and founded IPG Photonics.
Today, IPG has developed lasers with powers in excess of 100 kilowatts and offers the widest range of laser capabilities available. With a dedication to total control over product quality, we design and manufacture all key laser components to ensure IPG laser technology never compromises on performance.
IPG innovation continues to push the industry forward, offering fiber laser solutions with the reliability, energy efficiency, and capabilities necessary to support the most advanced applications around the world.
Advantages of IPG Fiber Laser Cutting Machine
Fast Cutting Speed
The speed at which an IPG fiber laser cutting machine cuts metal is higher than competing technologies. The 1 µm wavelength couples with higher efficiency than traditional lasers, and the excellent beam quality (focusability) of the IPG lasers provides greater energy density on the part, resulting in faster cutting.
High Availability
Unlike other laser technologies, IPG fiber lasers are zero maintenance. There are no consumable gases and no optics to align, so no preventative maintenance downtime. Utilizing rigorously tested long lifetime laser diodes and an entirely solid-state architecture, IPG fiber lasers have the best warranty in the industry.
Repeatable Process
Unlike competing lasers that may have poor short-term stability and suffer from long-term power degradation, IPG fiber lasers provide continuous repeatable performance. With power stability typically better than 0.5% of setting over 1000 hours of operation, you get the same cutting performance on every part.
Benefits of IPG Fiber Lasers
IPG fiber lasers are the most compact and energy efficient lasers on the market, added benefits include:
- Virtually maintenance free
- Reliably operates even in the harshest industrial environments including extreme vibration, dirt, humidity and temperature changes
- Flexible beam delivery supports easy production integration
- Delivers the widest breadth of output powers, wavelengths and modes of operation
- High flexibility in choosing operating parameters.
- 5-10 times more efficient in energy conversion than legacy CO2 lasers
- Wall plug efficiencies of 45% to over 50% exceed any alternative laser technologies
This unbeatable combination of benefits results in maximum productivity and the fastest ROI, making IPG fiber lasers industry standard and customer’s product of choice in numerous materials processing applications.
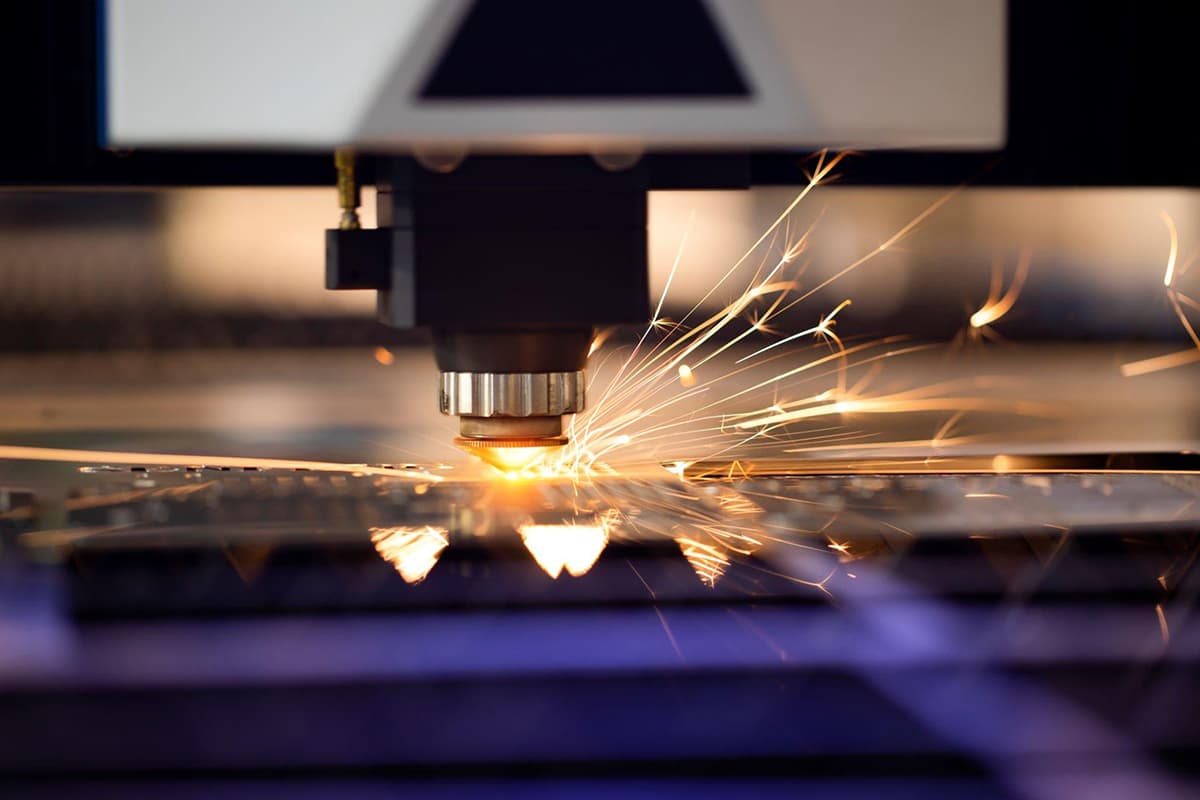
Types of Fiber Laser Sources
IPG offers diverse selection of fiber laser families across all modes of operation including continuous wave lasers, quasi-CW lasers, nanosecond pulsed lasers, ultrafast pico- and femtosecond pulsed lasers. IPG fiber lasers span the wavelength range from ultraviolet to Mid-IR and provide output powers from a few Watts to many kilowatts.
Continuous Wave (CW) Lasers
IPG offers a wide selection of continuous wave (CW) fiber lasers that can be integrated into laser systems, ranging in power from 10 W to tens of kilowatts. The primary use of CW lasers is to have the beam turned on for extended periods of time for continuous processing. However, IPG CW lasers can also be modulated at frequencies from a few kHz up to tens of kHz to provide pulsed laser processing in millisecond to microsecond pulse duration regime if required.
Quasi Continuous Wave (QCW) Lasers
IPG Quasi Continuous Wave (QCW) fiber lasers produce peak power 10 times greater in pulsed mode than when operating in CW mode, providing Joules of energy at pulse durations from 10 microseconds to 100 milliseconds. This makes QCW lasers ideal for high precision welding, fine cutting and drilling applications where high pulse energy is required to initiate or sustain laser-material coupling, but where parts may be sensitive to the heat produced in CW processing.
Pulsed Nanosecond Lasers
IPG offers pulsed nanosecond lasers spanning pulse durations from 1 to >1000 ns ranging in average output power from 10 W to 5 kW.
The laser beam quality can be optimized for fine micromachining or high speed surface treatment applications such as ablation, cleaning and texturing. The lasers span the wavelength range from ultraviolet and green to mid-infrared. Adjustable pulse duration options and variety of beam delivery, such as 2D and 3D scanners greatly enhance their versatility.
Ultrafast Lasers
In micromachining applications requiring small heat affected zone ultrashort pulse duration lasers are frequently used. Building on well-established expertise in pulsed fiber laser technology, IPG Photonics has developed ultrafast fiber lasers designed for precision micro-materials processing. IPG ultrafast fiber lasers utilize the intrinsic advantages of fiber laser technology allowing the most robust and cost effective laser tools. IPG ultrafast fiber lasers increase micro-machining throughout, improve reliability and eliminate cost barriers to ownership.
Adjustable Mode Beam (AMB) Lasers
YLS-AMB Adjustable Mode Beam Lasers provide independent programmable adjustment of the output beam mode to any combination of a small-spot high intensity bright core to a larger ring-shaped beam allows processing a wider range of material thicknesses and optimizes welding and cutting performance. Welding with AMB laser virtually eliminates spatter, reduces cracking and improves the overall finish. AMB lasers also provide better kerf quality when cutting thick mild steel.
High Peak Power (HPP) Lasers
The High Peak Power (HPP) option on YLR and YLS lasers enables running a CW laser in pulsed mode with up to 2X increase in peak power in comparison with CW average power. High Peak Power provides advanced processing capabilities for faster piercing, increased output quality, repeatability and waste reduction. HPP increases overall processing speeds, repeatedly drills clean holes and delivers high quality cuts of intricate parts with fine features while reducing overall laser power requirements. HPP also enhances drilling capabilities by allowing clean, controlled drilling in thicker materials. For cutting applications, this means shorter lead-ins and denser part nesting, which reduces material cost and waste.
Materials Processing By IPG Laser Solution
Lasers are a preferred tool for manufacturers across a broad variety of industries and applications. Offering high speed, energy efficient, and highly repeatable processing of metal and polymer parts, whether thick, thin, large, or small, IPG fiber laser solutions enable the optimized materials processing required for industrial production.
Laser Cutting
Laser cutting offers consistent high-quality cuts across a wide range of materials and thicknesses with lower kerf and thermal stress than traditional cutting methods. Powered by continuous or pulsed lasers that pierce cleanly and quickly, laser cutting suffers from no tool wear while providing accurate, clean cuts that make post-processing virtually unnecessary.
Laser Welding
Laser welding is a fast, economical, and non-contact method for joining a wide variety of metal-to-metal, polymer-to-polymer, metal-to-polymer, and glass-to-metal parts for virtually any industry or application. Processes requiring high processing speeds, complex weld geometries, or multi-layer joints benefit from the versatility and high productivity of laser welding.
Laser Cleaning
Laser cleaning, also known as laser ablation, is an environmentally-friendly process that requires no costly material handling like chemical cleaning or abrasive blasting. Lasers are non-contact and spatially selective, removing material only from the area required with a process that never degrades in quality.
Laser Heating & Drying
Wide area projection of laser energy is a highly efficient and sustainable heating, drying, and curing method for a variety of applications from battery foils to paint drying. Faster than traditional convection furnaces and more energy efficient than infrared lamps, laser heating and drying solutions offer the highest throughput and lowest operating costs in a compact footprint.
Laser Additive Manufacturing
Encompassing a variety of processes, including selective laser melting and sintering, laser metal fusion, and laser metal disposition, laser additive manufacturing (LAM) is a flexible, high-speed process suited for both prototyping and industrial production. LAM solutions offer high quality results in a wide variety of metals and non-metals, reducing the need for finishing processes, even for small or complex parts.
Laser Drilling
Laser drilling is a highly precise and repeatable process that can create holes of virtually any shape and size with diameters as small as a few microns. In many applications, laser drilling systems are able to drill hundreds or thousands of holes per second.
IPG Fiber Laser Cutting Machine Thickness and Speed Parameters
1. IPG/Carbon Steel/1000W-4000W
1000W | 1500W | 2000W | 3000W | 4000W | ||
Thickness | Speed | Speed | Speed | Speed | Speed | |
Material | (mm) | (m/min) | (m/min) | (m/min) | (m/min) | (m/min) |
1 | 9-12 | 9-12 | 9-11/18-22 | 9-12/25-30 | 9-11/40-50 | |
2 | 4.5-5 | 4.9-5.5 | 5-6 | 5-6/12-15 | 5-6/18-22 | |
3 | 3-3.3 | 3.4-3.8 | 3.7-4.2 | 4-4.5 | 4-4.5/15-18 | |
4 | 2.1-2.4 | 2.4-2.8 | 2.8-3.5 | 3.2-3.8 | 3.2-3.8/8-10 | |
Carbon Steel | 5 | 1.6-1.8 | 2.0-2.4 | 2.5-2.8 | 3.2-3.4 | 3-3.5/4-5 |
(O2/N2/Air) | 6 | 1.3-1.5 | 1.6-1.9 | 2.0-2.5 | 3-3.2 | 2.8-3.2 |
8 | 0.9-1.1 | 1.1-1.3 | 1.2-1.5 | 2-2.3 | 2.3-2.6 | |
10 | 0.7-0.9 | 0.9-1.0 | 1-1.2 | 1.5-1.7 | 2-2.2 | |
12 | 0.7-0.8 | 0.9-1.1 | 0.8-1 | 1-1.5 | ||
14 | 0.6-0.7 | 0.7-0.9 | 0.8-0.9 | 0.85-1.1 | ||
16 | 0.6-0.75 | 0.7-0.85 | 0.8-1 | |||
20 | 0.65-0.8 | 0.6-0.9 | ||||
22 | 0.6-0.7 |
2. IPG/Carbon Steel/6000W-12000W
6000W | 8000W | 10000W | 12000W | ||
Thickness | Speed | Speed | Speed | Speed | |
Material | (mm) | (m/min) | (m/min) | (m/min) | (m/min) |
1 | 10-12/ 45-60 | 10-12/ 50-60 | 10-12/ 50-80 | ||
2 | 5-6/ 26-30 | 5.5-6.8/ 30-35 | 5.5-6.8/ 38-43 | ||
3 | 4-4.5/ 18-20 | 4.2-5.0/ 20-25 | 4.2-5.0/ 28-30 | ||
4 | 3.2-3.8/ 13-15 | 3.7-4.5/ 15-18 | 3.7-4.5/ 18-21 | ||
5 | 3-3.5/ 7-10 | 3.2-3.8/ 10-12 | 3.2-3.8/ 13-15 | ||
6 | 2.8-3.2 | 2.8-3.6/ 8.2-9.2 | 2.8-3.6/ 10.8-12 | ||
8 | 2.5-2.8 | 2.6-3.0/ 5.0-5.8 | 2.6-3.0/ 7.0-7.8 | ||
Carbon Steel | 10 | 2.0-2.5 | 2.1-2.6/ 3.0-3.5 | 2.1-2.6/ 3.8-4.6 | 2.2-2.6 |
(O2/N2/Air) | 12 | 1.8-2.2 | 1.9-2.3 | 1.9-2.3 | 2-2.2 |
14 | 1-1.8 | 1.1-1.8 | 1.1-1.8 | 1.8-2.2 | |
16 | 0.85-1.5 | 0.85-1.2 | 0.85-1.2 | 1.5-2 | |
20 | 0.75-1.0 | 0.75-1.1 | 0.75-1.1 | 1.2-1.7 | |
22 | 0.7-0.8 | 0.7-0.85 | 0.7-0.85 | 0.7-0.85 | |
25 | 0.6-0.7 | 0.6-0.8 | 0.6-0.8 | 0.6-0.8 | |
30 | 0.4-0.5 | ||||
35 | 0.35-0.45 | ||||
40 | 0.3-0.4 |
Using the chart above, we can compare the parameters of different laser-cutting machines when cutting the same kind of material. For example:
- A 1000W laser cutting machine can cut 3mm-thick carbon steel at a maximum speed of 3.3m/min.
- A 1500W laser cutting machine can cut 3mm-thick carbon steel at a maximum speed of 3.9m/min.
- A 2000W laser cutting machine can cut 3mm-thick carbon steel at a maximum speed of 4.2m/min.
3. IPG/Stainless Steel/1000W-4000W
1000W | 1500W | 2000W | 3000W | 4000W | ||
Thickness | Speed | Speed | Speed | Speed | Speed | |
Material | (mm) | (m/min) | (m/min) | (m/min) | (m/min) | (m/min) |
1 | 12-15 | 16-20 | 20-28 | 30-40 | 40-55 | |
2 | 4.5-5.5 | 5.5-7.0 | 7-11 | 15-18 | 20-25 | |
3 | 1.5-2 | 2.0-2.8 | 4.5-6.5 | 8-10 | 12-15 | |
4 | 1-1.3 | 1.5-1.9 | 2.8-3.2 | 5.4-6 | 7-9 | |
Stainless Steel | 5 | 0.6-0.8 | 0.8-1.2 | 1.5-2 | 2.8-3.5 | 4-5.5 |
(N2) | 6 | 0.6-0.8 | 1-1.3 | 1.8-2.6 | 2.5-4 | |
8 | 0.6-0.8 | 1.0-1.3 | 1.8-2.5 | |||
10 | 0.6-0.8 | 1.0-1.6 | ||||
12 | 0.5-0.7 | 0.8-1.2 | ||||
16 | 0.25-0.35 |
4. IPG/Stainless Steel/6000W-12000W
6000W | 8000W | 10000W | 12000W | ||
Thickness | Speed | Speed | Speed | Speed | |
Material | (mm) | (m/min) | (m/min) | (m/min) | (m/min) |
1 | 60-80 | 60-80 | 60-80 | 70-80 | |
2 | 30-35 | 36-40 | 39-42 | 42-50 | |
3 | 19-21 | 21-24 | 25-30 | 33-40 | |
4 | 12-15 | 15-17 | 20-22 | 25-28 | |
5 | 8.5-10 | 10-12.5 | 14-16 | 17-20 | |
6 | 5.0-5.8 | 7.5-8.5 | 11-13 | 13-16 | |
8 | 2.8-3.5 | 4.8-5.8 | 7.8-8.8 | 8-10 | |
Stainless Steel | 10 | 1.8-2.5 | 3.2-3.8 | 5.6-7 | 6-8 |
(N2) | 12 | 1.2-1.5 | 2.2-2.9 | 3.5-3.9 | 4.5-5.4 |
16 | 1.0-1.2 | 1.5-2.0 | 1.8-2.6 | 2.2-2.5 | |
20 | 0.6-0.8 | 0.95-1.1 | 1.5-1.9 | 1.4-6 | |
22 | 0.3-0.4 | 0.7-0.85 | 1.1-1.4 | 0.9-4 | |
25 | 0.15-0.2 | 0.4-0.5 | 0.45-0.65 | 0.7-1 | |
30 | 0.3-0.4 | 0.4-0.5 | 0.3-0.5 | ||
35 | 0.25-0.35 | ||||
40 | 0.2-0.25 |
Next, we can compare the parameters of the laser cutting machines when cutting different types of materials. For instance:
- When cutting carbon steel that is 4mm thick, a a 1000W laser cutting machine has a maximum cutting speed of 2.4m/min.
- When cutting stainless steel that is 4mm thick, a 1000W laser cutting machine has a maximum cutting speed of 1.3m/min.
Overall, the chart and comparisons can help in selecting the appropriate laser-cutting machine based on the type and thickness of the material to be cut.
5. IPG/Aluminum/1000W-4000W
1000W | 1500W | 2000W | 3000W | 4000W | ||
Thickness | Speed | Speed | Speed | Speed | Speed | |
Material | (mm) | (m/min) | (m/min) | (m/min) | (m/min) | (m/min) |
1 | 10-13 | 14-18 | 20-28 | 30-40 | 40-55 | |
2 | 2.8-3.5 | 5.0-6.0 | 7-10 | 15-20 | 20-25 | |
3 | 2.0-2.6 | 4.5-6 | 8-10 | 13-15 | ||
4 | 1.4-1.6 | 2.5-3 | 5-6.5 | 7-9 | ||
Aluminum | 5 | 1.3-1.6 | 2.8-3.5 | 5-7 | ||
(N2) | 6 | 0.6-1 | 2-2.5 | 3-3.5 | ||
8 | 0.2-0.3 | 0.8-1.3 | 1.3-1.8 | |||
10 | 0.5-0.65 | 0.8-1 | ||||
12 | 0.3-0.45 | 0.6-0.8 | ||||
14 | 0.25-0.4 |
6. IPG/Aluminum/6000W-12000W
6000W | 8000W | 10000W | 12000W | ||
Thickness | Speed | Speed | Speed | Speed | |
Material | (mm) | (m/min) | (m/min) | (m/min) | (m/min) |
1 | 60-80 | 60-80 | 60-80 | 55-60 | |
2 | 28-35 | 38-43 | 39-42 | 35-40 | |
3 | 18-22 | 24-26 | 25-30 | 25-30 | |
4 | 10-14 | 15-17 | 20-22 | 20-25 | |
5 | 8-10 | 10-12 | 14-16 | 13-15 | |
6 | 4.5-6 | 6.7-7.5 | 10-13 | 10-12.0 | |
Aluminum | 8 | 2.0-2.8 | 3.2-4 | 7.8-8.8 | 5-6.0 |
(N2) | 10 | 1.2-1.5 | 2.6-2.8 | 5.2-7 | 3.4-4 |
12 | 0.7-0.95 | 1.7-2.0 | 3.5-3.9 | 2-2.8 | |
14 | 1.1-1.3 | 1.8-2.6 | 1.3-1.7 | ||
16 | 0.5-0.7 | 0.8-1.1 | 1.5-1.9 | 1.2-1.5 | |
20 | 0.3-0.35 | 0.65-0.8 | 1.1-1.4 | 0.8-1 | |
25 | 0.2-0.25 | 0.5-0.6 | 0.45-0.65 | 0.55-0.75 | |
30 | 0.4-0.5 | 0.4-0.5 | 0.3-0.45 | ||
35 | 0.25-0.35 | ||||
40 | 0.2-0.3 |
7. IPG/Brass/1000W-4000W
1000W | 1500W | 2000W | 3000W | 4000W | ||
Thickness | Speed | Speed | Speed | Speed | Speed | |
Material | (mm) | (m/min) | (m/min) | (m/min) | (m/min) | (m/min) |
1 | 15-18 | 22-30 | 26-40 | |||
2 | 4.5-5.5 | 10-14 | 15-20 | |||
3 | 3.2-3.8 | 5-7 | 8-12 | |||
Brass | 4 | 1.5-1.8 | 3-4 | 5-6.5 | ||
(N2) | 5 | 0.6-1 | 2-2.5 | 3-4 | ||
6 | 1.3-1.5 | 2.5-3 | ||||
8 | 0.5-0.8 | 1-1.5 | ||||
10 | 0.6-0.8 |
8. IPG/Brass/6000W-12000W
6000W | 8000W | 10000W | 12000W | ||
Thickness | Speed | Speed | Speed | Speed | |
Material | (mm) | (m/min) | (m/min) | (m/min) | (m/min) |
1 | 40-50 | 50-60 | 50-60 | 60-70 | |
2 | 21-24 | 28-33 | 34-38 | 35-40 | |
3 | 14-16 | 16-18 | 20-23 | 28-32 | |
4 | 10-11 | 11-13 | 14-17 | 18-24 | |
5 | 7.0-8.0 | 8.5-9.2 | 10-13 | 13-16 | |
Brass | 6 | 4.0-5.5 | 6.0-7.0 | 8.0-9.0 | 9-11 |
(N2) | 8 | 2.2-3.0 | 4.0-5.0 | 6.0-7.0 | 6-8 |
10 | 1.3-1.6 | 2.2-2.8 | 3.0-3.8 | 4.5-5.5 | |
12 | 0.7-0.9 | 1.2-1.5 | 1.7-2.2 | 3.1-3.6 | |
15 | 0.5-0.6 | 0.7-0.9 | 1.4-1.8 | ||
18 | 1.2-1.5 | ||||
20 | 1-1.3 |
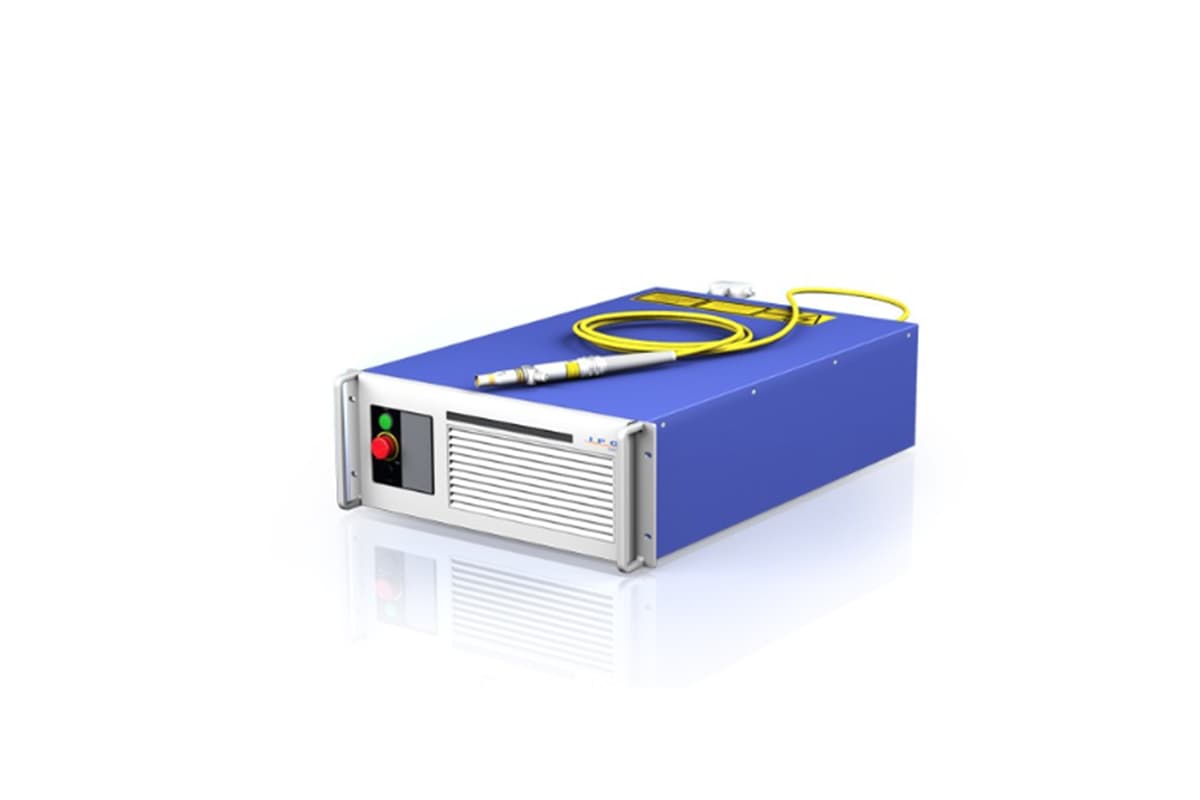
How to Choose the Right Laser Cutter Suit Your Needs
- Define Your Goals and Projects
Before diving into the selection of a laser cutter, it’s crucial to have a clear vision of your goals and the types of projects you plan to undertake. If your focus is primarily artistic, you may need a machine that offers high resolution and precision. On the other hand, if you’re thinking about large-scale production, cutting speed and efficiency will be critical factors.
Moreover, consider versatility as well. Are you planning to work mainly with wood, acrylic, metal, or other materials? Having a clear understanding of your goals will allow you to make more informed decisions during the selection process.
- Type of Material You Plan to Cut
The range of materials a laser cutter can handle is extensive, but not all machines are equal. Some are specialized in certain types of materials, while others are more versatile. Furthermore, if your projects involve a variety of materials, ensure that the laser cutter you’re considering is compatible with all of them.
From soft woods to resilient metals, each material has its own demands, and the machine should be able to adapt. Check the manufacturer’s specifications to ensure that the laser cutter can handle the diversity of materials you plan to use.
- Workspace Size and Cutting Dimensions
Workspace size and cutting dimensions are critical aspects in determining a machine’s versatility. Larger projects require a laser cutter with a substantial workspace. Additionally, check the maximum and minimum cutting dimensions the machine offers, as this can limit or expand your creative possibilities.
Imagine having to divide a large project into several smaller pieces due to size limitations. Choosing a laser cutter with an adequate workspace for your projects will allow you to work more efficiently and without unnecessary constraints.
- Laser Power and Cutting Speed
Laser power is a critical factor that directly influences a machine’s cutting capability. Thicker projects or denser materials will require higher power. It’s crucial to find the right balance between power and cutting speed to ensure optimal performance across a variety of projects.
If your projects involve intricate cuts on thinner materials, a machine with lower power but higher cutting speed might be more suitable. On the other hand, robust projects may require higher power for clean and efficient cuts.
- Software and User-Friendliness
The software associated with the laser cutter plays a crucial role in the user experience. Intuitive and user-friendly software can make a significant difference in project efficiency and quality. Ensure that the software allows easy import and editing of designs and check its compatibility with different file formats.
Moreover, some machines offer additional features, such as the ability to simulate cuts before executing them or the option to create designs directly in the software. These features can significantly enhance the laser cutter’s versatility and convenience.
- Safety Features
Laser cutters are powerful tools that require careful handling. Safety features are essential to protect the operator and prevent accidents. Ensure that the machine has effective emergency stop systems, protection against overheating, and other relevant safety features.
Additionally, some laser cutters are equipped with vision systems that detect foreign objects in the workspace, providing an additional layer of safety. Operator safety should be a priority when selecting a laser cutter.
- Cost and Value for Money
Budget is undoubtedly a determining factor when selecting a laser cutter, but it’s equally crucial to consider the value for money instead of solely focusing on the initial price. A more expensive machine may offer additional features, durability, and better long-term performance, justifying the investment.
Before making a decision based solely on the price, evaluate the build quality, manufacturer reputation, and specific features that the laser cutter offers. Consider the cost as a long-term investment rather than a one-time expense.
- Manufacturer’s Reputation and User Reviews
The manufacturer’s reputation and user reviews provide valuable insights into the quality and reliability of the laser cutter you’re considering. Research the manufacturer’s track record in the industry and look for feedback from users with similar needs.
Reviews can offer information on the machine’s long-term performance, build quality, customer support, and other critical aspects that may not be evident initially. Combining the manufacturer’s reputation with the experiences of previous users will give you a more comprehensive view of what to expect from the laser cutter.
In conclusion, when embarking on the journey to choose the perfect laser cutter, these considerations will guide you toward a selection that aligns with your goals and project requirements. Choose the perfect laser that meets your needs and unlocks new possibilities in your creative and manufacturing endeavors.