Press brake attachments are specialized tools and accessories designed to enhance the functionality of a press brake machine, allowing it to perform a wide range of bending and forming operations. These attachments, which include various dies, punches, and clamps, are essential for adapting the press brake to handle different materials, thicknesses, and bend angles with precision.
Choosing the right press brake attachment is crucial for any metalworking workshop. The correct attachment not only ensures that the machine operates efficiently but also improves the accuracy and consistency of the bends, which is vital for maintaining product quality. A well-suited attachment can reduce setup time, minimize errors, and increase production speed, ultimately boosting overall productivity. In contrast, the wrong attachment can lead to material waste, machine damage, or inefficient operations, negatively impacting your workshop’s efficiency and profitability.
What is a Press Brake Attachment?
A press brake attachment is a tool or accessory that is added to a press brake machine to enhance its capabilities and expand its range of applications in metal fabrication. These attachments are designed to perform specific tasks and enable the machine to bend, fold, or shape metal with greater precision and efficiency.
Press brake attachments come in various forms, each serving a unique purpose. Some common types of attachments include:
- Angle bending attachments: These attachments are used to bend metal at different angles, allowing for the creation of complex shapes and contours. They provide the flexibility to produce a wide range of products, from simple brackets to intricate architectural components.
- Hemming attachments: Hemming attachments are used to create hems or folds in metal. They ensure that the edges of a metal sheet are neatly folded over, providing a clean and finished appearance. Hemming attachments are commonly used in the production of automotive panels, HVAC ducts, and household appliances.
- Radius bending attachments: Radius bending attachments are used to create curved bends in metal sheets. They are ideal for applications that require smooth curves, such as architectural metalwork, decorative trim, and furniture components.
- Safety and productivity attachments: These attachments are designed to improve safety and enhance productivity in the metal fabrication process. Examples include laser safety systems, automatic tool changers, and material handling systems. These attachments reduce the risk of accidents, minimize downtime, and increase overall efficiency.
Press brake attachments offer numerous benefits, including increased productivity, improved accuracy, and reduced manual labor. By using these attachments, manufacturers can streamline their workflow, achieve faster production cycles, and meet the demands of their customers more efficiently. With the right combination of attachments, a press brake machine can become a versatile and indispensable tool in any metal fabrication shop.
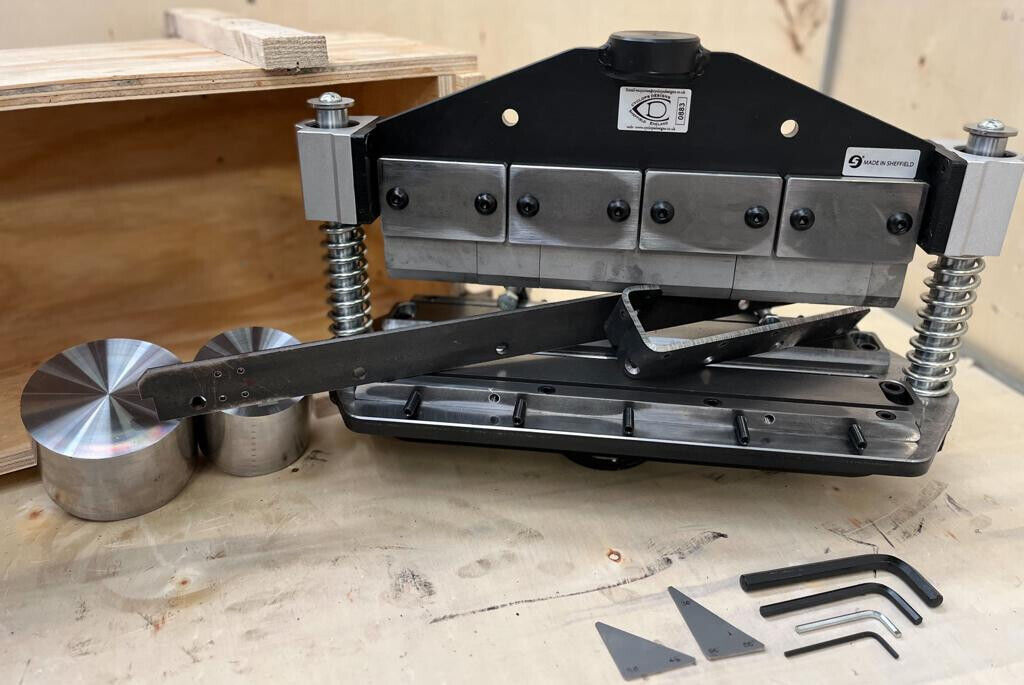
Understanding Press Brake Attachments
A press brake attachment refers to any additional tool or accessory that can be installed on a press brake machine to expand its functionality and versatility. These attachments are designed to perform specific tasks such as bending, forming, and shaping metal sheets or plates with precision. They allow the press brake to handle a wide variety of materials and thicknesses, ensuring the desired bends and forms are achieved efficiently.
Common Types of Press Brake Attachments
- Bending Dies: These are the most commonly used attachments and are essential for forming metal into various angles. Different types of dies include:
- V-dies: Used for general bending operations, they come in different sizes to handle various bend angles and radii.
- Gooseneck Dies: Designed for deeper bends and complex shapes without interfering with the workpiece.
- Hemming Dies: Used for creating clean folds or edges in sheet metal, especially for joining parts together.
- Multi-V Dies: These versatile dies have multiple V-grooves, allowing for various bending options in one tool.
- Punches: Punches work in conjunction with dies to press the metal into the desired shape. They come in different forms, such as flat, angled, or gooseneck, depending on the specific bending needs.
- Clamps: These attachments secure the workpiece in place during bending, ensuring precision and reducing the chances of errors.
- Guards and Backgauges: These are safety and alignment accessories that help guide the workpiece into the correct position for accurate bending, while also protecting the operator from accidents.
How Attachments Enhance Efficiency and Production Capacity
Using the right press brake attachments significantly improves the efficiency and production capacity of a workshop. Specialized dies and punches allow operators to perform complex bending tasks without requiring additional manual adjustments or setups, reducing downtime and increasing the speed of production. Attachments like multi-V dies or hemming dies enable versatile operations, meaning fewer tool changes are needed during production runs. This results in higher throughput and lower operating costs.
In addition, clamps and backgauges ensure that each bend is consistent and precise, minimizing material waste and ensuring product quality. By investing in the correct attachments, workshops can tackle a wider range of jobs, improve flexibility, and meet varying customer demands efficiently.
Benefits of Using a Press Brake Attachment
Using a press brake attachment offers numerous benefits in metal fabrication. Here are some of the key advantages:
- Enhanced Productivity: Press brake attachments help streamline the metal fabrication process, allowing for faster production cycles. These attachments automate certain tasks, reducing the need for manual labor and increasing overall productivity.
- Improved Accuracy: Press brake attachments are designed to provide precise bending and shaping of metal sheets. With the use of these attachments, manufacturers can achieve consistent and accurate results, ensuring high-quality finished products.
- Expanded Range of Applications: By adding different press brake attachments, manufacturers can increase the capabilities of their machines and expand the range of applications. Whether it’s angle bending, hemming, or radius bending, these attachments enable the creation of complex shapes and designs.
- Cost Savings: Press brake attachments eliminate the need for additional machinery or tools for specific bending requirements. This not only saves on equipment costs but also reduces the space required for multiple machines. By maximizing the use of a single press brake machine with various attachments, manufacturers can save money and optimize their production space.
- Improved Safety: Many press brake attachments come with safety features that protect operators from accidents and injuries. These features include guards, sensors, and interlocks that ensure safe operation. By using these attachments, manufacturers can create a safer working environment for their employees.
Overall, incorporating press brake attachments into metal fabrication processes can significantly improve productivity, accuracy, and safety while also offering a cost-effective solution for a wide range of bending requirements.
Factors to Consider When Choosing a Press Brake Attachment
Selecting the right press brake attachment involves analyzing various factors that affect the machine’s performance and the quality of the final product. Below are the key considerations:
1. Material Type
High-strength materials like stainless steel require more durable attachments, such as hardened V-dies, to withstand the higher tonnage needed for bending. In contrast, softer metals like aluminum are more susceptible to marking or damage during bending, so special non-marring tools or urethane-covered dies are often used to protect the surface finish. Other materials, such as copper or brass, have unique properties that may necessitate custom tooling to prevent cracking or deformation during the bending process, ensuring a clean and precise result.
Each material also has different spring-back characteristics, so choosing the right attachment ensures proper compensation for this.
2. Thickness and Tonnage
Material thickness plays a crucial role in attachment selection. The thicker the material, the higher the tonnage (force) required to bend it properly. Here’s how it impacts attachment choice:
For thinner materials, precision and minimal deformation are crucial, so smaller V-dies and precision-ground punches are typically used. When working with thicker materials, larger V-dies and heavy-duty punches are necessary to handle the increased tonnage. Additionally, the press brake must have the appropriate tonnage capacity to avoid damaging the attachment or the machine itself, ensuring efficient and safe operation.
Failing to match the attachment to the material’s thickness can lead to poor bending results, tool damage, or safety risks.
3. Bending Requirements
Different bending processes require specific attachments, and your production needs should dictate the choice of tools:
V-bending, the most common method, typically uses V-dies available in various sizes and angles based on the required bend. Air bending allows for greater flexibility in bend angles, as the material does not fully contact the die, and requires a V-die and punch for versatility with fewer tools. Bottom bending, on the other hand, demands full contact between the workpiece and the die, offering enhanced precision and tighter tolerances with specialized bottoming dies. For unique operations such as hemming, offset bends, or coining, specific dies and punches are essential to achieve the desired results.
4. Production Volume
Your workshop’s production volume directly affects attachment selection:
For high-volume production, durable and versatile attachments that can endure repetitive cycles without wearing down are crucial. Multi-V dies, for example, enable multiple bends with fewer tool changes, boosting efficiency. In contrast, for low-volume or custom jobs, flexibility is essential. Adjustable or quick-change tooling is advantageous in these cases, allowing for varied operations on different materials without significant downtime.
5. Precision and Accuracy
The level of precision required for your products also determines the type of attachment you should choose:
For high-precision work that requires tight tolerances, investing in precision-ground punches and dies is crucial, as these tools provide greater accuracy and minimize variability in bends. For less demanding jobs, standard tools can be sufficient, offering a balance between cost and quality while still achieving acceptable results.
In summary, the right press brake attachment can optimize your metalworking process, ensuring that your machine delivers the desired results for your specific materials, bending needs, production volumes, and precision requirements.
Matching Attachments to Your Press Brake Machine
When selecting press brake attachments, it’s essential to match them with your machine’s specifications and capabilities to ensure optimal performance:
- Understanding Your Machine’s Specifications: Knowing your press brake’s tonnage, working length, and pressure capacity is fundamental. Tonnage refers to the maximum force the machine can apply, which must align with the demands of the attachments. Working length determines the size of the workpieces the machine can handle, affecting the types of dies and punches that can be used. Pressure capacity is crucial for ensuring that the attachments can operate within the machine’s limits without causing damage.
- Compatibility of Attachments: Ensure that the attachments are compatible with your press brake’s brand and model. Different brands or models may have varying mounting systems, dimensions, and design features. Proper fit is essential to avoid issues during operation and to ensure that the attachments function as intended.
- Choosing Between Automated vs. Manual Attachment Setups: Decide whether to use automated or manual attachment setups based on your production needs. Automated setups offer convenience and speed, reducing manual intervention and allowing for quicker changes between different attachments. Manual setups provide more flexibility for custom or smaller-scale jobs but may require more time for tool changes. Balancing these options based on your workshop’s volume and complexity of tasks will help optimize your operations.
Installing a Press Brake Attachment
When it comes to installing a press brake attachment, there are a few key steps to follow.
First, it’s important to ensure that the attachment is compatible with your existing press brake machine. Check the specifications of both the attachment and the machine to ensure they are a good match.
Next, carefully read the manufacturer’s instructions for installation. These instructions will provide you with step-by-step guidance on how to properly install the attachment.
Before installation, make sure to gather all the necessary tools and equipment. Having everything you need on hand will help streamline the installation process and prevent any unnecessary delays.
Once you’re ready to begin, it’s important to take safety precautions. Wear appropriate personal protective equipment (PPE) such as gloves and safety glasses to protect yourself during the installation process.
Follow the instructions provided by the manufacturer to attach the press brake attachment to your machine. This may involve securing bolts, aligning components, and making any necessary adjustments. Take your time to ensure everything is properly installed and secure.
After installation, it’s important to test the attachment to ensure it is working correctly. Follow the manufacturer’s instructions for testing and make any necessary adjustments if needed.
Remember, if you are uncertain or uncomfortable with the installation process, it’s always best to consult a professional or reach out to the manufacturer for assistance.
By following these steps and taking the necessary precautions, you can successfully install a press brake attachment and enhance the capabilities of your machine.
Cost and Budget Considerations
When selecting press brake attachments, it's important to carefully consider cost and budget to ensure a good return on investment (ROI) while meeting your production needs:
- Weighing Attachment Cost Against Return on Investment (ROI): Evaluate the cost of attachments relative to the benefits they provide. Consider how the attachment will impact your workshop’s productivity, accuracy, and overall efficiency. A higher initial investment may be justified if the attachment significantly improves production speed, reduces errors, or extends the lifespan of your press brake machine, leading to greater long-term savings and profitability.
- Considering Long-Term Usage and Replacement Costs: Assess the durability and maintenance needs of the attachments. Higher-quality attachments may have a higher upfront cost but can offer greater longevity and reduced maintenance expenses. Consider how often the attachments will need to be replaced or serviced and factor these costs into your budget to avoid unexpected expenses and ensure consistent performance.
- Evaluating Whether High-End Attachments Can Boost Overall Production Efficiency: Determine if investing in high-end attachments will provide significant improvements in production efficiency. Advanced attachments with enhanced features may offer greater precision, versatility, and speed, which can lead to increased output and reduced downtime. Weigh these potential gains against the initial cost to decide if the investment aligns with your production goals and financial constraints.
Troubleshooting Common Issues with Press Brake Attachments
I’ve encountered a few common issues when using press brake attachments, but don’t worry – there are simple troubleshooting steps you can take to resolve them. Let’s take a look at some of these issues and how to tackle them:
- Misalignment: One of the most common issues with press brake attachments is misalignment. This can occur when the attachment is not properly installed or when the machine is not calibrated correctly. To troubleshoot this issue, start by checking the alignment of the attachment and make any necessary adjustments. Also, ensure that the machine is calibrated according to the manufacturer’s specifications.
- Material Slippage: Another issue that can arise is material slippage, where the material being bent slips out of position during the bending process. This can be caused by insufficient clamping pressure or improper tooling. To troubleshoot this issue, check the clamping pressure and adjust it if needed. Additionally, make sure that the tooling is appropriate for the material being bent and consider using anti-slip devices or lubrication to prevent slippage.
- Inaccurate Bends: Sometimes, press brake attachments can result in inaccurate bends, leading to parts that do not meet the required specifications. This can be caused by factors such as incorrect tooling, improper machine settings, or worn-out tooling. To troubleshoot this issue, double-check the tooling to ensure it is suitable for the desired bend, verify the machine settings, and replace any worn-out tooling if necessary.
- Safety Concerns: While press brake attachments can enhance productivity and expand the capabilities of the machine, it is crucial to address any safety concerns that may arise. Common safety issues include improper guarding, inadequate training, and lack of awareness of safety procedures. To troubleshoot safety concerns, ensure that the machine and attachment have appropriate guarding in place, provide comprehensive training to operators, and regularly reinforce safety protocols.
Remember, troubleshooting press brake attachment issues requires careful attention to detail and adherence to safety protocols. By addressing these common issues, you can ensure smooth operation and maximize the benefits of your press brake attachment without the need for a conclusion.
Conclusion
By utilizing press brake attachments effectively, fabricators can optimize their metal fabrication processes, improve efficiency, and achieve high-quality results. With the right attachment and proper installation, fabricators can take their press brake machine to the next level and unlock new possibilities in their metal fabrication projects.