Have you ever marveled at how flat metal sheets can be transformed into intricately designed parts? If so, you've likely encountered the remarkable capabilities of a punch press. A vital tool in the metal fabrication industry, the punch press is engineered to shape or cut material by exerting pressure through a die or tool. The outcome? Precisely formed metal pieces, all achieved with exceptional productivity. Let's explore the fascinating realm of the punch press.
Table of Contents
What Is A Punch Press
A punch press is a machine used in metalworking and fabrication processes to shape or cut materials using a die or tool. It operates by applying force to the material through the use of a ram, which forces the die or tool through the workpiece. The die or tool can have various shapes and configurations, allowing for a wide range of forming and cutting operations.
Punch presses are commonly used in industries such as automotive manufacturing, aerospace, construction, and electronics to produce a variety of parts and components. They are capable of creating intricate shapes, holes, and patterns in metal sheets with high precision and efficiency.
There are different types of punch presses, including mechanical, hydraulic, and pneumatic presses, each with its own advantages and applications. Mechanical punch presses use mechanical mechanisms, such as flywheels and gears, to generate force, while hydraulic punch presses use hydraulic systems to exert pressure. Pneumatic punch presses, on the other hand, use compressed air to power the punching action.
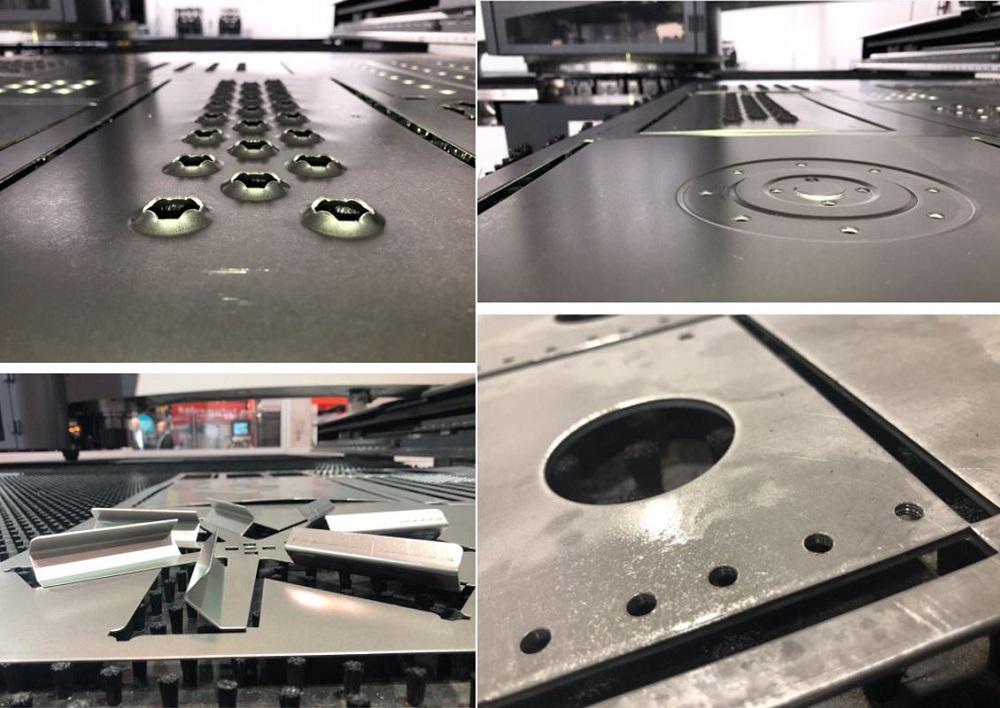
Types of Punch Press Machine
- Flywheel Drive Punch Press:
- Pros:
- Stable energy consumption: Ensures consistent energy use during operations.
- Cost-effective: Generally lower in price compared to more advanced models.
- Simple maintenance: Fewer complexities mean easier upkeep.
- Cons:
- Limited force control: The force remains constant, which may not be suitable for diverse tasks.
- Not ideal for precision work: Best suited for standard operations rather than intricate designs.
- Pros:
- Mechanical Drive Punch Press:
- Pros:
- Consistent force: Guarantees uniformity in output.
- Durability: Built for heavy-duty applications and prolonged use.
- Reliability: Minimal risk of unexpected downtime or malfunctions.
- Cons:
- Limited speed adjustability: May not be suitable for tasks requiring variable speeds.
- Higher operating costs: Due to its heavy-duty nature, it consumes more energy.
- Pros:
- Hydraulic Drive Punch Press:
- Pros:
- Variable force and speed: Provides flexibility in operations.
- Precision: Ideal for tasks requiring precise punches.
- Safety: Hydraulic systems incorporate built-in emergency brake mechanisms.
- Cons:
- Maintenance: Requires regular checks on the hydraulic system.
- Higher initial investment: Precision and flexibility come at a premium.
- Pros:
- Servo Drive Turret Punch Press:
- Pros:
- Versatility: Swiftly switch between tools, minimizing downtime.
- High accuracy: Servo motors ensure each punch is precise.
- Energy efficiency: Power consumption occurs only during punching.
- Cons:
- Price: More costly than traditional punch presses.
- Skilled operators required: Its features necessitate expertise and experience.
- Pros:
- CNC Punch Press:
- Pros:
- High precision: Achieves precise punches consistently.
- Repeatability: Ensures uniform results across batches.
- Automation: Decreases manual intervention, boosting productivity.
- Cons:
- Higher cost: Advanced technology commands a premium price.
- Complexity: Requires operators proficient in CNC operations.
- Pros:
When choosing a punch press machine, it's essential to consider factors such as the specific requirements of your applications, budget constraints, desired precision, and production volume. Each type of machine offers unique features and capabilities, so selecting the right one depends on your individual needs and priorities.
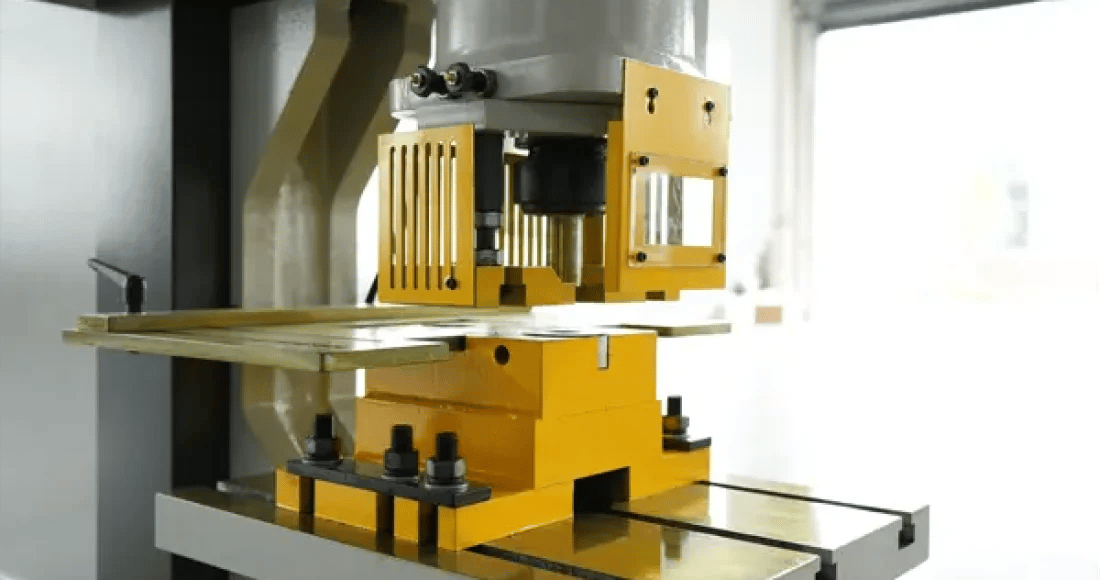
How Does A Punch Press Work
- Preparation: Before operating the punch press, the appropriate die or tool must be selected and installed on the machine. The workpiece is then positioned securely on the machine's bed or table.
- Activation: The operator activates the punch press, typically by engaging a control panel or foot pedal. This initiates the machine's operation.
- Clamping: If necessary, the machine's clamping mechanism secures the workpiece in place to prevent movement during the punching process.
- Punching: The ram of the punch press descends towards the workpiece, carrying the die or tool with it. The die/tool applies force to the workpiece, deforming it to create the desired shape or cutting it to size.
- Retraction: After completing the punching operation, the ram retracts to its original position, allowing the operator to remove the finished workpiece and prepare for the next cycle.
- Repeat: The process is repeated for each workpiece until the desired quantity has been produced.
The operation of a punch press can vary depending on the specific type of machine and its features. For example, some punch presses may have automatic feeding mechanisms to streamline the process, while others may offer additional functionalities such as bending or forming capabilities.
Why Your Shop Need A Punching Machine
Precision and Repeatability
A standout feature of punch presses, including the turret punch press, is their incredible precision. Every stroke operation is meticulously controlled, and the results are not just precise but also highly repeatable. This ensures that even in mass production, each workpiece comes out with the same high level of accuracy.
- Tooling and Die Configurations: The machine’s tooling and die configurations offer a range of designs, shapes, and sizes. This diverse set allows manufacturers to create multiple identical units without variations in shape or size.
- Reliability and Control: The hydraulic ram and the hydraulic cylinder, integral parts of a punch press, ensure consistent force application. Such reliability is vital, especially when dealing with materials that demand a specific pressure or force for optimal results.
Production Speed and Efficiency
Speed and efficiency define the performance of a punch press. For businesses focusing on large-scale production, investing in a punch press is economical in the long run due to its high production speed.
- Cycle and Operation: Every operation, from the movement of the turret to the ram deceleration and the return action, is optimized for minimal time wastage. The processes are streamlined, ensuring faster production cycles.
- Automation and Productivity: Modern punch presses integrate CNC technology, increasing automation and reducing the need for manual interventions. This not only boosts productivity but also ensures consistency across all produced units.
Versatility in Materials and Shapes
The turret punch press and other types of punch presses can handle a broad range of materials, from sheet metal to thicker steel plates. Their versatility doesn’t stop at materials alone.
- Material Diversity: From air-thin sheets to more substantial steel plates, punch presses exhibit a broad range of material handling capacity. This versatility ensures that industries with varied needs can rely on this singular machine for multiple applications.
- Shape Creation: The intricate tooling and die systems support the creation of different shapes and patterns. Whether it’s round holes or more complex designs, a punch press can deliver with precision.
Economical Aspects and Operating Costs
Large-scale production often comes with increased costs. However, the punch press, with its design and efficiency, proves to be an economical choice for manufacturers.
- Power Consumption and Energy Efficiency: Modern punch presses, especially those with hydraulic systems, have optimized power consumption. The hydraulic ram, combined with a stable drive system, ensures that energy is used efficiently, leading to reduced operating costs.
- Maintenance and Longevity: With features like an emergency brake system and a robust frame structure, these machines promise durability. Their design minimizes wear and tear, reducing maintenance costs over time.
Additional Advantages to Consider
Beyond the core benefits, punch presses offer a plethora of other advantages that further solidify their position in the industry.
- Noise Control: Unlike some heavy machines, punch presses have mechanisms that control noise levels. This makes them more suitable for environments where noise pollution can be a concern.
- Safety Features: The design of the machine takes into account potential accidents. Features such as pinch points, stopping mechanisms, and emergency braking systems ensure the safety of operators.
- Customizability: Manufacturers today offer punch presses that can be customized based on specific industry needs. From varying tonnage capacity to different types of drive shafts and motors, the customization options are vast.
What's the Cost of Punch Press
The cost of a punch press can vary significantly based on its type, capacity, and features. On average:
- Small, manual punch presses: $500 to $5,000.
- Mid-range, with more features: $10,000 to $50,000.
- High-end, CNC or industrial grade: $100,000 and above.
KRRASS Punch Press Technology
Selecting the right punching machine is pivotal for operational success:
- Evaluate your requirements: Understand the type of work and materials you’ll handle.
- Consider machine capacity: Ensure it matches your production needs.
- Assess precision needs: For intricate designs, opt for higher precision machines.
- Determine the available space: Machines come in varying sizes.
- Budget: Find a balance between requirements and available funds.
KRRASS's Punch Press technology offers a transformative approach to optimizing production. With a focus on productivity, customization, and user-friendly options, our innovative solutions are tailored to meet the real needs of our customers. Beyond traditional offerings, our commitment to excellence drives us to provide avant-garde solutions that boost productivity, enhance efficiency, and address unique demands. Explore how our Stamping Press technology can revolutionize your manufacturing operations, streamline your processes, and elevate your success to unprecedented levels.
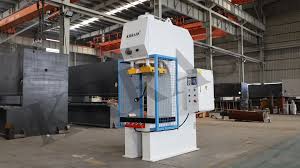