Sheet metal roll bending is an indispensable technique in the world of metal fabrication. This process enables the creation of intricate, curved shapes from metal sheets, bars, and tubes by gradually rolling the material through a series of rollers. Whether it’s forming simple arcs or more complex cylindrical structures, sheet metal roll forming plays a crucial role in industries such as construction, automotive, aerospace, and manufacturing.
In this article, we’ll explore the different aspects of metal sheet roll bending, including the various types of rolling methods like three-roll bending, four-roll bending, and pyramid rolling. We’ll also delve into the wide range of applications, from creating curved panels for architectural projects to manufacturing structural components for heavy machinery. Additionally, we’ll discuss the key advantages of metal rolling, such as its ability to handle large sheets and achieve uniform curves, making it ideal for both large-scale and precision projects.
However, it’s important to note that the technique has its limitations, including potential material deformation and thickness constraints, which may require additional processes or specialized equipment. So, let’s dive deeper into the world of metal roll forming to understand its full potential and challenges!
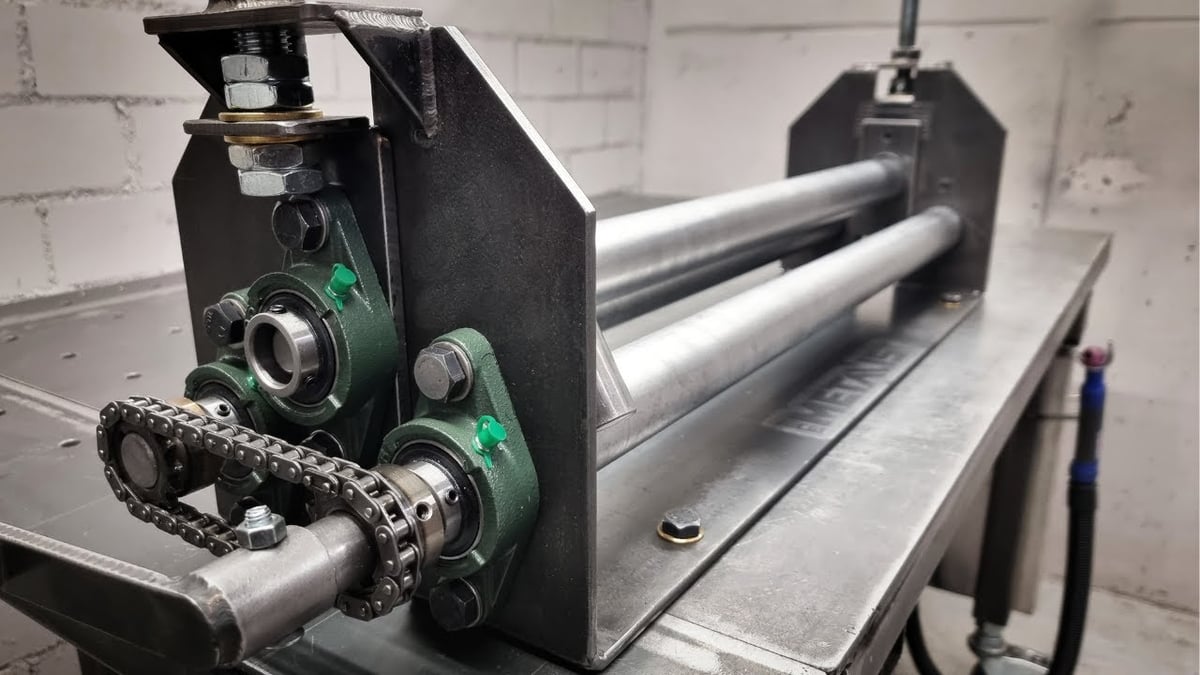
What is Sheet Metal Roll Bending?
Roll bending, also known as plate rolling or angle bending, is a metalworking process that uses a series of rollers to bend a metal piece into a specific curve or radius. The metal is forced through the rollers, progressively applying pressure to shape the material into the desired curvature. This process is commonly used for manufacturing pipes, tanks, and other cylindrical or conical shapes.
Different Types of Sheet Metal Roll Bending
Sheet metal roll bending can be performed using a variety of methods, each suited for different shapes, materials, and production requirements. Here are the main types of sheet metal roll bending processes:
- Three-Roll Bending
This is the most common method of roll bending, using three rollers to gradually curve the metal sheet. The top roller applies pressure while the bottom two rollers provide support and drive the sheet forward. It’s ideal for creating cylindrical or curved shapes like tubes, pipes, and large cylindrical tanks. - Four-Roll Bending
Similar to three-roll bending, this method includes an additional roller, which helps in controlling the process more precisely. The four-roll machine allows for better control over the rolling process and can also pre-bend the edges of the sheet before the full rolling process. This is useful for achieving higher precision and reducing material waste. - Pyramid Roll Bending
In this method, the rollers are arranged in a pyramid formation, with one roller at the top and two at the bottom. It’s mostly used for thicker metal sheets that need heavier rolling forces. The pyramid formation offers stability and is often used in heavy-duty metal fabrication. - Plate Rolling
Plate rolling involves bending metal sheets into cylindrical shapes. It’s often used to create large-diameter pipes or structural components for industrial applications. Plate rolling can be done with a range of materials and is commonly employed in industries like oil and gas, shipbuilding, and construction. - Pinch Roll Bending
In this type, two of the rollers "pinch" the metal sheet while the third roller bends it. Pinch roll bending is known for its ability to form tight curves and smaller-diameter cylinders, making it suitable for delicate or precision metalworking.
Each type of sheet metal roll bending has its unique strengths and applications, allowing manufacturers to select the best technique for their specific project needs.
Applications of Sheet Metal Roll Bending
Roll bending is a highly versatile technique used across various industries due to its ability to shape metal into precise, curved forms. Here are some of the key applications of roll bending:
Pressure Vessels
Industries like petrochemical, power generation, and food processing use roll bending to create pressure vessels. These vessels are essential for containing fluids or gases at high pressure, and roll bending ensures the metal sheets are accurately curved to handle the internal stresses.
Architectural and Structural Components
Roll bending is extensively used in the construction and architectural industries to create curved beams, arches, and metal frames. These components are commonly used in modern building designs, bridges, stadiums, and other infrastructure projects.
Pipelines and Tubes
The oil and gas industry relies on roll bending for the production of large-diameter pipes and tubes, which are essential for transporting fluids and gases over long distances. Roll bending helps create seamless curves in metal sheets, which are later welded into pipes.
Automotive Parts
Roll bending plays a significant role in the automotive industry, where curved components like exhaust systems, bumpers, and frames require precise bending. It ensures these parts are manufactured with consistent quality, strength, and accuracy.
Aerospace Industry
In aerospace, roll bending is used to form lightweight but strong components such as airframe structures, wings, and fuselage sections. The ability to roll bend lightweight metals like aluminum ensures the production of aerodynamic shapes crucial for flight efficiency.
Metal Tanks and Silos
Industries such as agriculture, food processing, and chemical manufacturing use roll bending to produce large cylindrical tanks and silos. These tanks are used for storage of liquids, chemicals, and grains, and roll bending ensures that the structures are both durable and accurate.
Shipbuilding
Roll bending is key in shipbuilding for creating large, curved metal sheets used in the hulls, decks, and various structural components of ships. The process allows for precision forming of metals that must withstand harsh marine environments.
Renewable Energy
In the renewable energy sector, roll bending is used to manufacture components for wind turbines, solar panels, and other green technologies. For example, the tower sections of wind turbines often require large-scale roll bending to create their cylindrical forms.
Railway and Transportation Equipment
Roll bending is used in the production of rail tracks, car bodies, and other curved metal components that are essential for the safe and efficient operation of trains and other transportation vehicles.
Advantages of Roll Bending
Roll bending offers several significant benefits over other metalworking techniques, making it a preferred choice in various industries:
- Versatility:
Roll bending machines can handle a wide range of materials, including steel, aluminum, and various alloys, as well as different thicknesses. This adaptability makes them suitable for numerous applications, from architectural components to heavy machinery parts. - Efficiency:
The roll bending process is relatively quick, allowing for high production rates. Compared to other metal bending techniques, such as press brake bending, roll bending can efficiently produce large quantities of curved components with minimal downtime. - Precision:
Roll bending can achieve tight radii and complex curves with impressive accuracy. Advanced roll bending machines are equipped with digital controls and measurement systems that ensure consistent results, making them ideal for applications requiring exact specifications. - Minimal Material Waste:
The precise nature of roll bending results in minimal material waste. Unlike other bending techniques that may require excess material for shaping, roll bending effectively utilizes the material, reducing costs and environmental impact. - Strong Structural Integrity:
Roll bending maintains the strength of the material being processed. Unlike other methods that can weaken or distort the metal, roll bending preserves the structural integrity of the metal, ensuring that the final product is durable and reliable. - Production of Large Parts:
Roll bending is particularly effective for producing large and heavy components that would be challenging to form using other methods. This capability is essential in industries like construction and shipbuilding, where large structural elements are common.
Limitations of Roll Bending
Despite its many advantages, roll bending has a few limitations that can affect its suitability for certain applications:
- Material Limitations:
Some materials, such as brittle metals or those that are extremely hard, may not be suitable for roll bending. These materials can crack or break during the bending process, leading to product failures or increased production costs. - Initial Investment:
The cost of roll bending machines can be high, particularly for advanced models equipped with automation and precision controls. This initial investment can be a barrier for small businesses or those with limited budgets, making it difficult to adopt this technology. - Skilled Operators Required:
Operating a roll bending machine requires a certain level of skill and experience. While the machines are user-friendly, mastering the intricacies of the bending process may necessitate additional training for staff, which can involve time and expense. - Size Limitations:
While roll bending can produce large parts, the size of the machine can limit the maximum dimensions of the components that can be formed. Larger parts may require specialized equipment or modifications to existing machinery. - Setup Time:
Although the bending process itself is efficient, the initial setup time for roll bending machines can be significant, especially when switching between different materials or shapes. This can lead to delays in production if not managed properly.
Understanding these advantages and limitations helps manufacturers make informed decisions about whether roll bending is the right choice for their specific metal fabrication needs.
How Does a Metal Plate Bending/Rolling Machine Work?
Achieving the desired shape of a metal plate using a metal plate bending/rolling machine involves four essential steps:
- Setting the Bending Force According to the Desired Radius
- Positioning the Metal Plate on the Table to Ensure Uniform Bending/Rolling
- Pre-Pinching/Pre-Bending the Edges of the Metal Plate
- Passing the Metal Plate Through the Bending/Rolling Machine
Step 1: Setting the Bending Force on the Machine
The process begins with the bending operator assessing the workload of the metal plate bending/rolling machine. After evaluating the specifics, the operator determines the appropriate bending force needed to shape the metal plate to the desired Inside Diameter (ID) or Outside Diameter (OD). This decision is crucial, as it directly impacts the final result.
Step 2: Positioning the Metal Plate on the Table
Once the bending force is established, the operator places the metal plate on the machine’s table. This step is critical for restricting any unwanted movement of the plate during the bending process. Proper positioning ensures that the metal plate remains stable, preventing misalignment or incorrect bends.
Step 3: Pre-Pinching/Pre-Bending the Edges
Before initiating the main bending process, pre-pinching or pre-bending involves bending the edges (tails) of the metal plate. This initial step is vital for achieving the desired radius at the edges and also minimizes the need for adjustments after the main bending operation, streamlining the overall process
Step 4: Bending the Workpiece Using the Machine
With the metal plate securely positioned and the pre-bending completed, the operator can proceed to place the plate between the top roller and the bottom rollers of the bending machine. This final bending stage is crucial, and having an experienced operator is essential, as metal plate bending/rolling machines represent a significant investment for any workshop. The operator’s expertise ensures precise and effective bending, resulting in high-quality metal components.
Types of Machines Used for Sheet Metal Bending/Rolling Operations
Across various industries worldwide—such as shipbuilding, metal fabrication, wind energy, earthmoving, metal structures, rocket shell production, oil tanks, and tubes and pipes—metal plate bending/rolling machines play a crucial role in fabricating diverse equipment and metal structures.
The following types of plate bending/rolling machines are commonly utilized in these industries for their bending operations:
- 2-Roll Plate Bending/Rolling Machine
- 3-Roll Plate Bending/Rolling Machine
- 4-Roll Plate Bending/Rolling Machine
These machines can be further categorized into two types based on their guideway design:
- Linear Guideway Plate Bending/Rolling Machine
- Swing Guideway Plate Bending/Rolling Machine
Different industries require specific machines tailored to their operational workload. The choice of machine also depends on the required precision levels and, significantly, the skill set of the operators. Selecting the right equipment ensures optimal performance and efficiency in metal bending processes.
Tips for Bending/Rolling Sheet Metal
Whilst bending sheet metal is a useful strategy for many different types of projects, sheet metal bends can be easy to mess up if you get the technique wrong. To ensure you create the professional bend you are after, follow these helpful tips.
Tip 1: Choose the Right Materials
Due to some metals being more malleable than other metals, you need to be aware of the use of heat, and if it is necessary to reduce any cracking and weakening of the material.
Materials That Work Well for Sheet Metal Bends:
- Galvanised steel: A resilient and corrosion-resistant metal. If you bend galvanised steel, it can be moulded into the appropriate shape for your project. The bending process is usually quite simple, and in most cases, galvanised steel will be more malleable than shaped stainless steel forms.
- 5052 Aluminium: With high workability as well as low weight, aluminium is easy to bend as it is extremely malleable. This makes cracking rare.
- Stainless Steel: Mostly used for manufacturing within the food and medical industries, it has corrosion resistance, with some grades excelling at resistance. Different grades of stainless steel will perform differently but it can be prone to work hardening.
- Spring steel: Can be malleable when annealed but, once the work has hardened, it tends to require heat in order to bend again.
- Copper: This tends to be very malleable. Its antimicrobial benefits also give copper an added edge.
- Mild steel: No heat tends to be required for mild steel, making it very malleable.
Tip 2: Avoid Bending to a Sharp Internal Corner
It’s important to avoid bending to a sharp internal corner when producing sheet metal bends because it could cause cracking or weakening of the metal. This can be avoided by having a radius on your tool.
PRO TIP: The thickness of the material you’re producing should be the same as the inside bend radius.
Tip 3: Use a Press Brake
Brakes are extremely useful for creating a clean bend, as the metal won’t be wavy or even warped.
The two biggest advantages of a mechanical press brake have to be the speed and accuracy it offers when bending sheet metal.
Tip 4: Protect the Surfaces
Take care of the appearance of your metal by avoiding scratching its surface.
PRO TIP: The best way to avoid scratches is to use masking tape anywhere that might come into contact with something hard. Similarly, you could also use wood blocks to protect the section when bending.
Tip 5: Bend Allowance
Bending metal involves pushing, pulling, or stretching the material. Therefore, you need to calculate the bend allowance because this will offer you reliable numbers to work from when you lay out a flat sheet.
Certain factors need to be considered with this, such as material thickness and internal radius size.
Bend allowance is compensation for what happens to the material when it is stretched and formed from a flat pattern into the desired bend. By working out this bend allowance, you can figure out how much of a flange will remain when you’ve made the desired bend.
Quality Sheet Metal Bends with Lrrass Machinery
KRRASS is a comprehensive sheet metal fabrication company dedicated to delivering top-notch solutions. Our expert team collaborates with organizations nationwide to produce high-quality fabricated metal products while ensuring an outstanding customer experience.
At KRRASS, we offer a full range of CNC machining services and take pride in providing both complete sheet metal fabrication and subcontracting services.