In the realm of industrial manufacturing, laser cutting has revolutionized precision and efficiency. Understanding the speed capabilities of a 3kW laser cutter is crucial for optimizing production processes and achieving superior results. This article delves into the fundamental question: What is the speed of 3kW laser cutting? By exploring the technological boundaries and practical considerations, we uncover how manufacturers can harness this capability to push the limits of productivity and precision in metal fabrication.
Table of Contents
What Is Laser Cutting
Laser cutting is a precise slitting process capable of cutting various metallic and non-metallic materials of different thicknesses. It operates by guiding, shaping, and focusing a laser beam that, upon contact with the workpiece, heats the material to the point of melting or vaporization. The laser beam concentrates its entire power onto a small spot, often less than half a millimeter in diameter. When the heat introduced exceeds what the material can conduct away, the laser penetrates through, initiating the cutting process.
Unlike other methods that use large-scale tools with significant force applied to the sheet metal, laser cutting occurs without direct contact. This approach prevents tool wear and eliminates deformities or damage to the workpiece. The result is a clean, precise cut, making laser cutting highly efficient for producing intricate shapes and achieving high-quality finishes in industrial manufacturing.
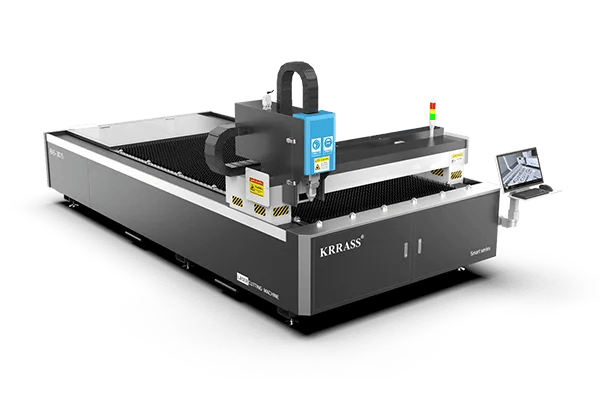
What Are Advantages of Laser Cutting
Versatile Material Range
Laser cutting encompasses a wide spectrum of materials commonly used in industrial processing, ranging from robust metals like steel, aluminum, and stainless steel to non-ferrous metals. Additionally, non-metal materials such as plastics, glass, wood, and ceramics can also be safely and effectively cut with lasers. This versatility extends to varying material thicknesses, spanning from as thin as 0.5 millimeters to over 30 millimeters. This expansive capability positions laser technology as the premier cutting tool across numerous applications, whether in metals or non-metals, due to its ability to deliver high-quality results consistently.
Freedom in Cutting Contours
Laser cutting utilizes a focused beam that heats the material locally, minimizing thermal stresses across the rest of the workpiece. As a result, the kerf—the width of the cut—is narrow and precise, allowing for the smooth cutting of complex and intricate contours without burrs. This precision reduces the need for extensive post-processing, making laser cutting efficient and ideal for applications requiring small lot sizes, a wide range of variants, and prototype construction. Its flexibility and ability to deliver clean, high-quality cuts make it a preferred choice in modern manufacturing.
High-quality cutting edges with ultrashort pulses
Ultrashort pulse lasers operate by vaporizing materials so rapidly that they minimize heat influence, resulting in exceptionally high-quality cutting edges devoid of melted material ejection. This capability makes these lasers ideal for manufacturing intricate metal products, including medical technology components like stents. In industries such as display manufacturing, ultrashort pulse lasers are also employed to cut chemically hardened glass with precision and efficiency. This advanced technology underscores its versatility and effectiveness in producing superior, clean cuts across various industrial applications.
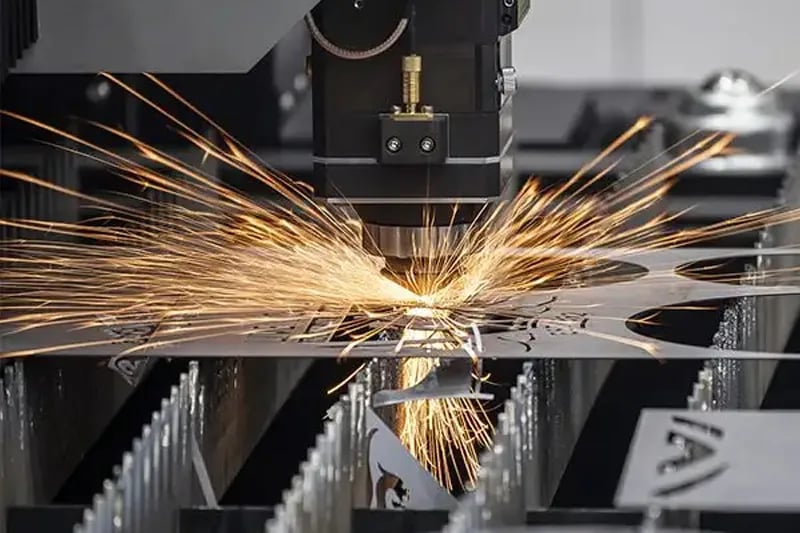
Exploring Different Types of Laser Cutters
Laser cutters vary significantly in their capabilities and applications, catering to diverse material cutting needs across industries. Understanding these distinctions is crucial when choosing the right tool for your specific requirements.
Gas Laser Cutter
For precision cutting of non-metal materials such as wood, acrylic, or fabric, the gas laser cutter stands out. This type utilizes a CO2 laser operating at a higher wavelength, delivering clean and accurate cuts on various non-metal materials. Whether you need intricate designs etched onto wood or precise fabric patterns for fashion, the gas laser cutter excels in these applications.
Crystal Laser Cutter
Offering versatility across both metals and non-metals like glass, plastic, and wood, the crystal laser cutter utilizes neodymium-doped yttrium aluminum garnet (nd) or neodymium-doped yttrium ortho-vanadate (nd) lasers. Despite its higher initial cost, this solid-state laser cutter provides flexibility for a wide range of cutting tasks, making it a valuable investment for multifaceted manufacturing needs.
Fiber Laser Cutter
Known for its exceptional versatility and longevity, the fiber laser cutter is a preferred choice for various materials including metal, wood, glass, and plastic. With an impressive lifespan of approximately 25,000 hours—significantly longer than other types—the fiber laser cutter offers durability and cost-effectiveness. Its powerful beam, 100 times stronger than gas lasers, ensures efficient cutting processes across industries, from manufacturing components to crafting intricate designs on diverse materials.
Choosing the right laser cutter depends on your specific material requirements and operational needs, ensuring optimal performance and productivity in your manufacturing processes.
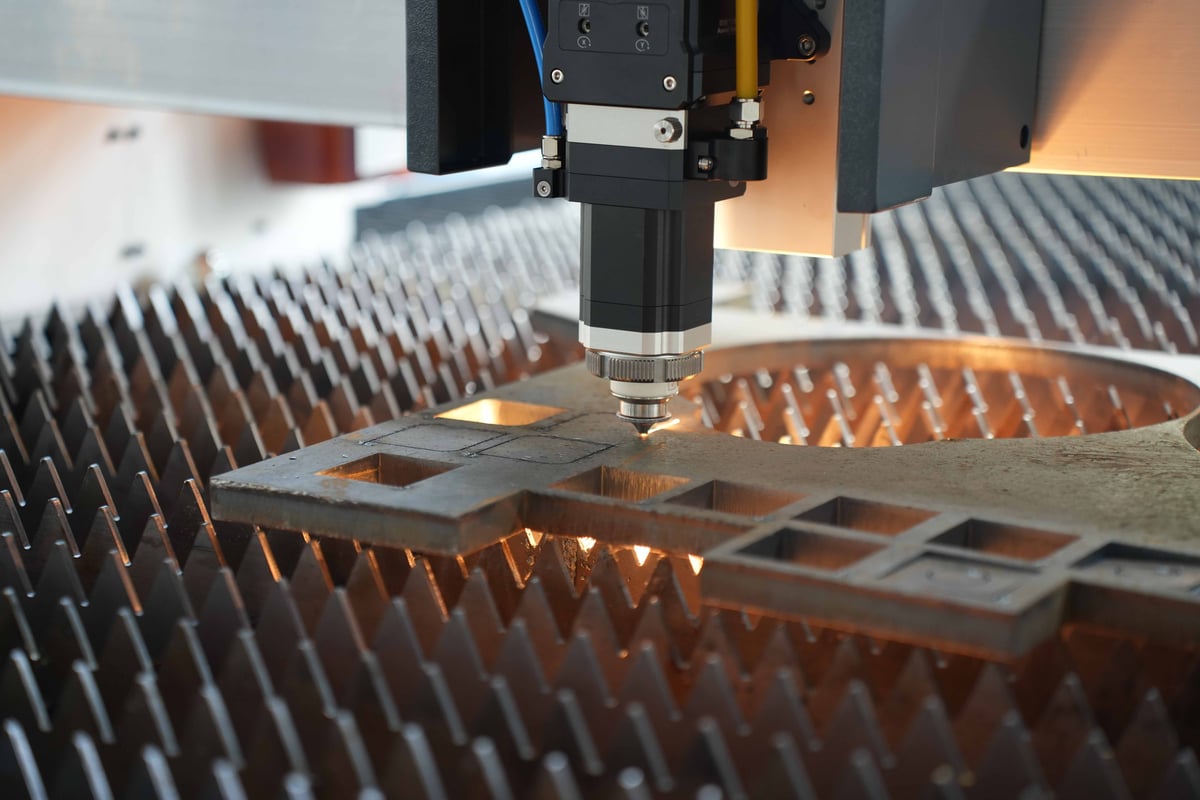
Introduction to 3kW Laser Cutting Technology
In the realm of industrial manufacturing, laser cutting stands as a cornerstone technology known for its precision and versatility. Central to its efficiency is the critical factor of cutting speed, particularly in applications utilizing 3kW laser cutting technology. This introduction explores the pivotal role of cutting speed in industrial settings, provides an overview of 3kW laser cutting technology, and underscores the importance of optimizing this parameter for maximizing efficiency and maintaining high-quality standards in production processes.
Laser cutting's ability to swiftly and accurately process various materials has revolutionized manufacturing across sectors. With a focus on 3kW laser systems, which offer a balanced blend of power and precision, this discussion delves into how optimizing cutting speed not only enhances throughput but also ensures the integrity and consistency of finished products. Understanding these dynamics is crucial for industries seeking to streamline operations and achieve competitive advantages through advanced laser cutting capabilities.
What Is the Speed of 3kw Laser Cutting?
3000W fiber laser cutting machine for cutting different materials at a maximum speed of 35m/min for carbon steel; Stainless steel with a high speed of 35m/min; Aluminum plate with a high speed of 43m/min; Copper plate with a high speed of 35m/min;
The cutting speed of different materials using a 500W fiber laser cutting machine is 13m/min for carbon steel; Stainless steel with a high speed of 14m/min; Aluminum plate with a high speed of 5.5m/min; Copper plate with a high speed of 5.5m/min;
1000W fiber laser cutting machine for cutting different materials at a maximum speed of 24m/min for carbon steel; Stainless steel with a high speed of 24m/min; Aluminum plate with a high speed of 10m/min; Copper plate with a high speed of 10m/min;
2000W fiber laser cutting machine for cutting different materials at a maximum speed of 28m/min for carbon steel; Stainless steel with a high speed of 28m/min; Aluminum plate with a high speed of 25m/min; Copper plate with a high speed of 16m/min;
What Is the Cutting Thickness of 3kw Laser Cutting?
The maximum cutting thickness of a 3KW laser cutter depends on the material being cut. Here's a look at some common materials and their maximum cutting thicknesses: carbon steel: 20–22 mm, stainless steel: 10–12 mm, aluminum: 8–10 mm, brass: 6 mm.
3KW and 6KW Fiber Lasers: Laser Cutting Capabilities Comparison
1. Cutting Thickness:
When it comes to cutting thickness, the power of a laser cutter significantly impacts its capabilities:
- A 3kW laser cutter can efficiently cut up to 18mm of carbon steel, 8mm of stainless steel, and 8mm of aluminum.
- In comparison, a 6kW laser cutter extends these capabilities to 22mm of carbon steel, 18mm of stainless steel, and 16mm of aluminum.
2. Cutting Speed and Efficiency:
The choice of laser power also affects cutting speed and efficiency differently across materials:
- Stainless Steel and Aluminum: Higher wattage lasers noticeably improve cutting speed and overall cutting quality. The increased power facilitates faster processing times and enhances the precision of cuts on these materials.
- Carbon Steel: While higher wattage lasers increase cutting speed by approximately 15%, the most significant improvement lies in the cutting quality. This ensures cleaner cuts and minimal thermal distortion, crucial for maintaining product integrity in industrial applications.
3000W | 6000W | ||
Material | Thickness | speed m/min | speed m/min |
Carbon steel | 1 | 8.0–10 | 8–10 |
2 | 5.0–6.5 | 5–6 | |
3 | 4.0–5.0 | 3.5–4.5 | |
4 | 3.5–4.2 | 3.2–3.8 | |
5 | 2.6–3.5 | 3.0–3.6 | |
6 | 2.5–3.2 | 4.2–5.0 | |
8 | 1.8–2.6 | 3.5–4.2 | |
10 | 1.4–2.0 | 2.2–2.8 | |
12 | 1.2–1.6 | 1.8–2.3 | |
14 | 0.9–1.2 | 1.2–1.8 | |
16 | 0.8–1.0 | 0.8–1.3 | |
18 | 0.6–0.8 | 0.6–0.9 | |
20 | 0.5–0.8 | ||
22 | 0.4–0.8 | ||
Stainless steel | 1 | 30–40 | 42–52 |
2 | 17–24 | 20–33 | |
3 | 8.0–10 | 15–22 | |
4 | 4.5–6.0 | 10–15 | |
5 | 3.0–4.0 | 8.0–12 | |
6 | 2.0–3.5 | 6.8–8.0 | |
8 | 1.5–1.7 | 3.0–4.0 | |
10 | 2.0–2.5 | ||
12 | 0.8–1.5 | ||
14 | 0.6–0.8 | ||
16 | 0.5–0.8 | ||
18 | 0.4–0.6 | ||
Aluminum N2 | 1 | 25–38 | 42–55 |
2 | 15–18 | 20–40 | |
3 | 6.5–8.0 | 15–25 | |
4 | 3.5–5.0 | 9.5–12 | |
5 | 2.5–3.5 | 5.0–8.0 | |
6 | 1.5–2.5 | 3.8–5.0 | |
8 | 0.7–1.0 | 2.0–2.5 | |
10 | 1.0–1.5 | ||
12 | 0.8–1.0 | ||
16 | 0.5–0.8 |
How To Improve Cutting Speed of Fiber Lasers
As domestic laser technology matures and breaks the price monopoly held by foreign counterparts, manufacturers of laser cutting machines in China are expanding their market presence. This trend reflects a growing demand for laser cutting machines across various industries.
The flexibility of laser cutting in processing metals has gained recognition among sheet metal customers for its superior cutting speed compared to traditional equipment. Speed, as a fundamental factor in efficiency, plays a crucial role in maximizing usage efficiency during operations.
Factors Affect Cutting Speed
Variety of Materials
Laser cutting machines handle a range of metal materials, including aluminum, stainless steel, carbon steel, copper, and alloys. Each material possesses unique characteristics and absorbs laser energy differently, influencing cutting speeds even at the same thickness.
Diverse Thicknesses
Material thickness directly impacts laser cutting performance. Thicker materials require more laser energy and consequently slower cutting speeds. This variation in thickness affects perforation times and overall processing efficiency during cutting operations.
Impact of Output Power
Output power is a critical determinant of cutting speed. Higher laser power levels translate to increased laser energy, facilitating faster cutting speeds for thinner materials. Here are examples illustrating the relationship between power and cutting speeds across different materials:
- Low Power (e.g., 1kW): Suitable for thinner materials with moderate cutting speeds.
- Medium Power (e.g., 3kW): Provides balanced performance for a wide range of materials, including stainless steel and aluminum.
- High Power (e.g., 6kW and above): Ideal for thick materials, offering rapid cutting speeds and enhanced efficiency.
Understanding these factors enables manufacturers to optimize laser cutting processes, adjusting parameters like power and material handling to achieve maximum efficiency and quality in metal fabrication. By leveraging these insights, businesses can meet diverse production demands effectively in today's competitive industrial landscape.
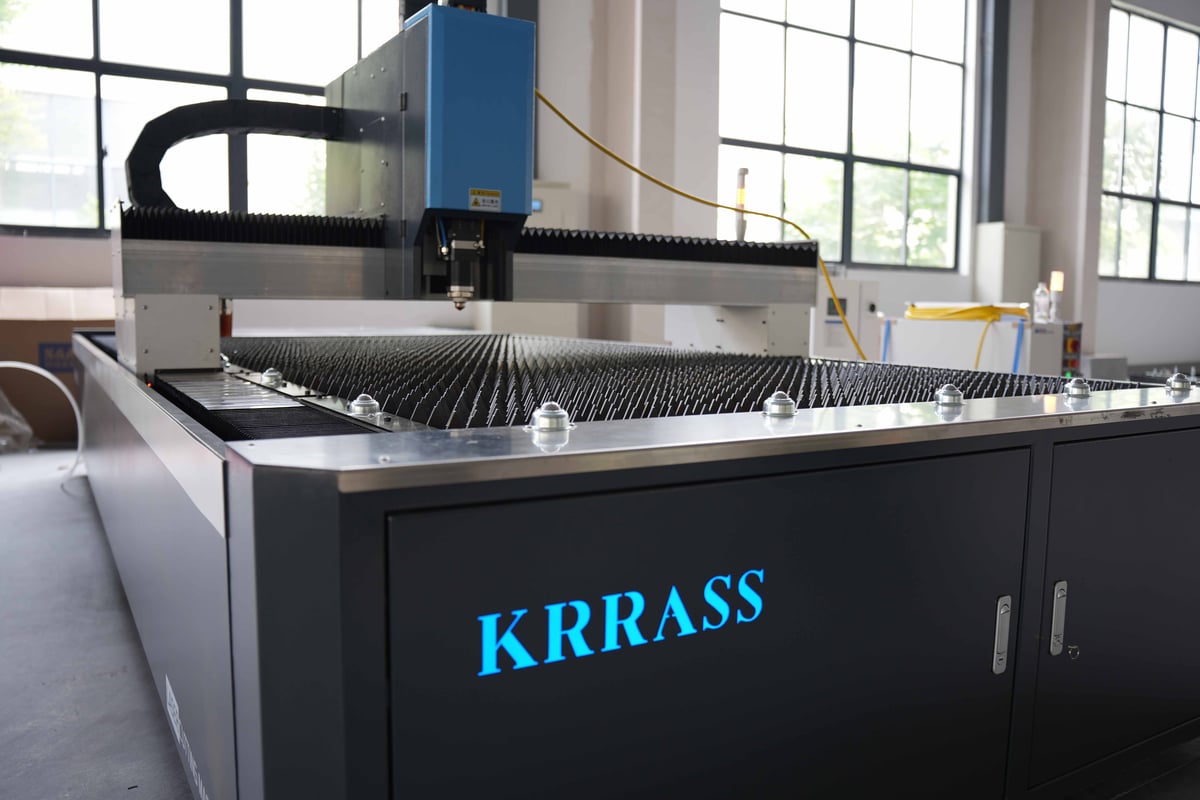
Strategies for Enhancing Laser Cutting Machine Speed
Improving the cutting speed of laser cutting machines involves optimizing machine parameters, which significantly influence performance. Proper parameter adjustments are akin to fine-tuning a vehicle's gears for smooth operation and efficiency. Here are key areas to focus on when optimizing these parameters:
Initial Speed:
The initial speed setting determines how quickly the machine starts its cutting process. Contrary to common belief, a higher initial speed isn't always better. Setting the initial speed too high can lead to excessive machine vibration, affecting cutting precision and stability.
Acceleration:
Acceleration refers to how quickly the machine reaches its cutting speed from the initial start. Similar to the throttle in a car, optimal acceleration ensures efficient transitions between cutting patterns. Setting acceleration too low may slow down the machine's cutting speed during complex patterns or frequent starts and stops.
5 Tips for Enhancing Laser Cutting Precision
Achieving precise laser cuts requires attention to detail and careful adjustments. Here are five essential tips to improve laser cutting accuracy:
1. Optimize Material Settings
Selecting the right settings for your materials is crucial for achieving accurate cuts. Each material type—whether wood, metal, or acrylic—has specific characteristics that affect laser cutting performance. Adjust your machine settings accordingly, ensuring optimal cutting parameters to avoid issues like reduced accuracy or potential hazards.
2. Fine-tune Cutting Speeds and Power
Finding the perfect balance between cutting speed and power intensity is key to achieving precise laser cuts. Experiment with different settings on test pieces before proceeding with your main project. This process helps determine the ideal combination for efficient cutting without compromising quality due to excessive heat or inadequate penetration.
3. Utilize a Smaller Laser Beam Spot
The size of the laser beam spot significantly impacts cutting precision. Opt for shorter focal length lenses to generate a smaller, more concentrated beam spot. This finer spot size allows for intricate detailing and sharp edges in your designs, enhancing overall cutting accuracy.
4. Ensure Mirror Alignment
Proper alignment of laser machine mirrors is essential for maintaining a clear and uninterrupted beam path. Misaligned mirrors can lead to inconsistent cutting results and wasted materials. Regularly check and adjust mirror alignments to ensure precise laser beam delivery throughout the cutting process.
5. Stabilize Your Workbench
A stable workbench is vital for achieving consistent laser cutting accuracy. Vibrations or instability in your work surface can cause misalignments and affect the quality of your cuts. Invest in a sturdy workbench that provides a solid foundation for your laser cutter, minimizing operational disturbances and maximizing precision.
By implementing these tips, you can enhance the accuracy and efficiency of your laser cutting operations, ensuring high-quality results across a variety of materials and designs. Each adjustment contributes to achieving impeccable cuts, meeting the demands of intricate projects and industrial applications with confidence.
About KRRASS from China
KRRASS, a distinguished brand within the laser industry, stands as a leader in laser technology innovation and application. Renowned for its pioneering contributions, KRRASS is recognized globally for delivering authoritative laser processing solutions.
At KRRASS, we specialize in providing comprehensive solutions for intelligent manufacturing. Our offerings include advanced laser intelligent machines, precision measurement tools, automated production lines, and smart factory construction services. These integrated solutions empower industries worldwide to enhance productivity, efficiency, and quality across their manufacturing processes.
With a commitment to innovation and customer satisfaction, KRRASS continues to lead the way in shaping the future of laser technology, supporting diverse industrial sectors in achieving their operational excellence goals.
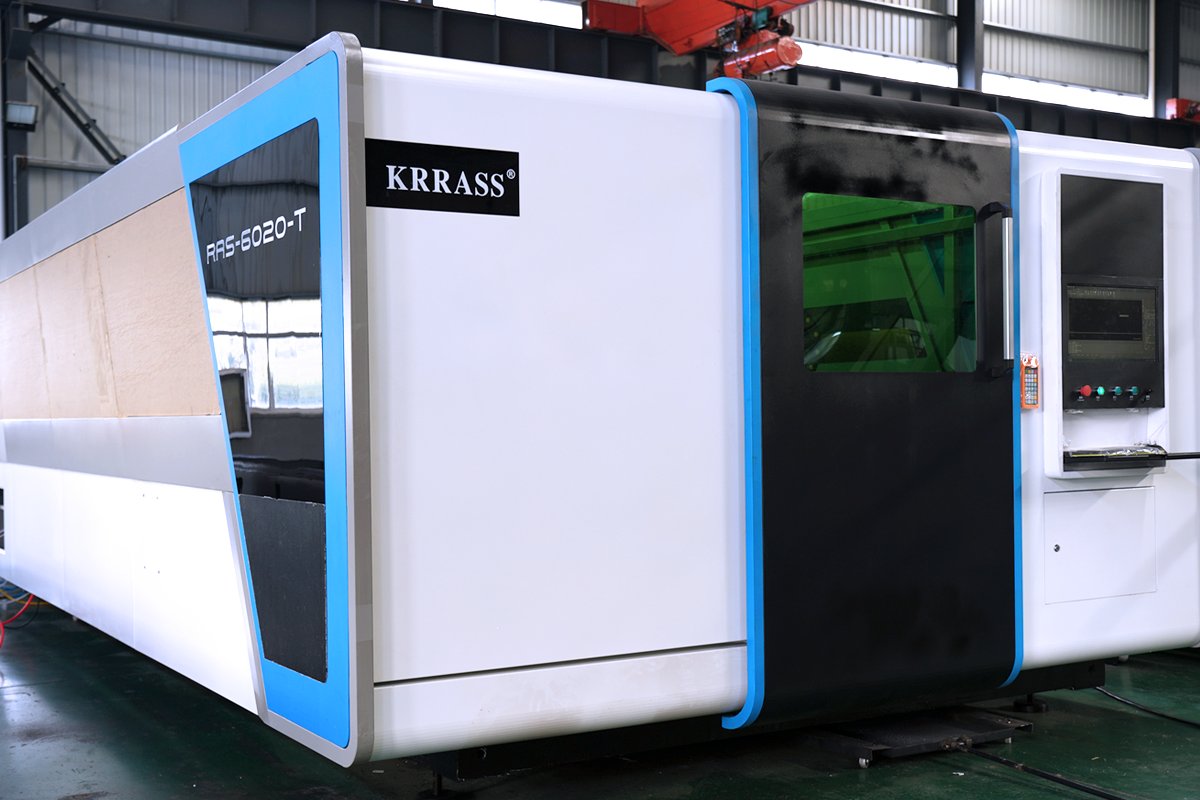