Press brakes are essential machines in metal fabrication, used to bend, fold, and shape sheet metal into precise forms. By applying force through a punch and die system, they create a wide range of angles and shapes, making them vital for industries such as automotive, aerospace, and manufacturing. Traditionally, press brakes operate horizontally, but there’s a specialized type known as the vertical press brake, which performs these functions in a vertical orientation. This design is significant for industries requiring high precision, space efficiency, and the ability to work on smaller or more intricate parts. Vertical press brakes offer enhanced versatility and precision in specific applications, making them an ideal choice for workshops with limited floor space or complex bending requirements.
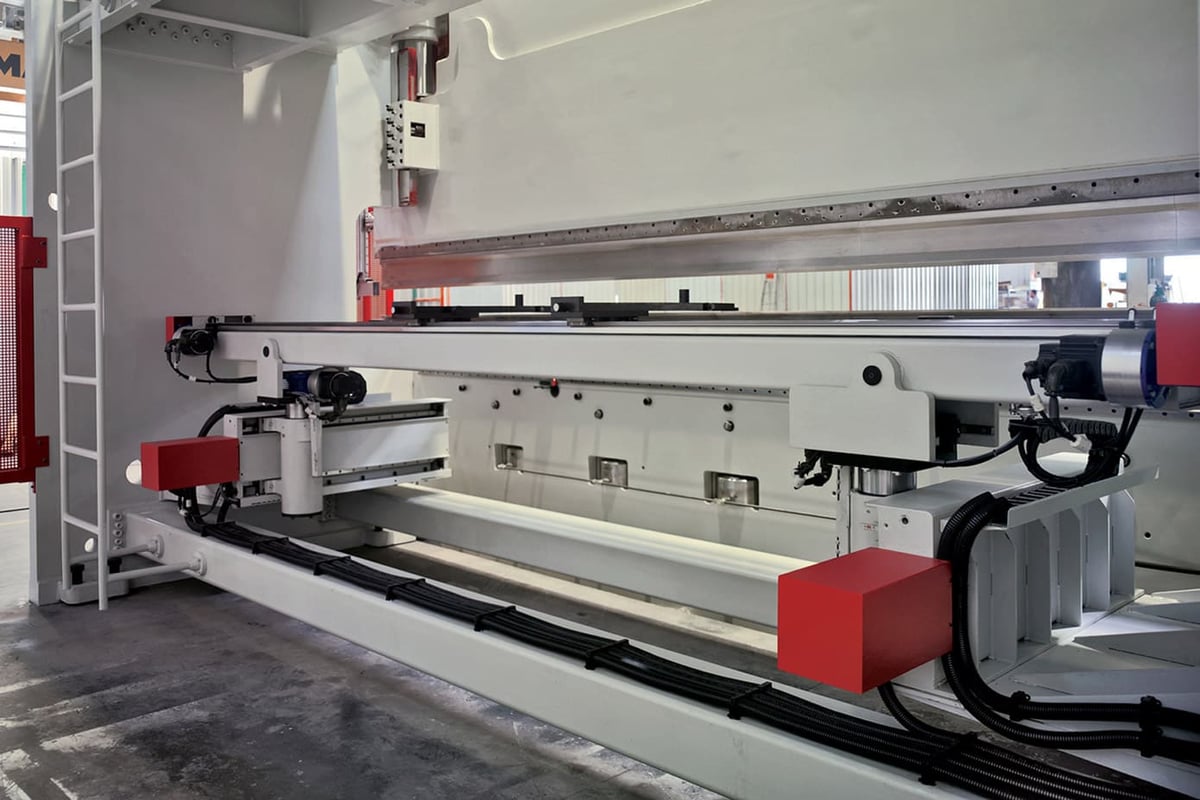
What Is Vertical Press Brake
A vertical press brake is a type of press brake machine designed for bending and shaping sheet metal in a vertical orientation. Unlike traditional horizontal press brakes, where the bending action occurs along a horizontal plane, a vertical press brake operates with a vertical press action.
How Vertical Press Brakes Work
Vertical press brakes operate by using a vertical pressing action, where the upper die moves downward in a vertical direction to bend the metal sheet against a stationary lower die. This vertical movement allows for high precision and control, making it ideal for creating intricate bends, tight tolerances, or working on smaller workpieces. The operator positions the metal sheet between the dies, and the machine applies force to bend it at the desired angle.
Comparison with Traditional Horizontal Press Brakes
While horizontal press brakes are the most common type, where the metal is bent along a horizontal plane, vertical press brakes offer unique advantages. The vertical orientation takes up less floor space, which is a significant benefit for workshops with limited room. Additionally, the vertical motion can offer better precision for detailed or complex bends, making it ideal for tasks that require exact angles or delicate materials.
Key Components and Their Functions
- Upper and Lower Dies: These are the primary tools used in the bending process. The upper die presses down vertically on the workpiece, while the lower die provides support and determines the bend shape.
- Ram: The ram is the component that drives the upper die downward, applying the necessary force for the bending operation.
- Frame: The frame supports the machine and provides stability during the pressing action, ensuring accurate and consistent bends.
- Control System: Many vertical press brakes feature computerized controls (CNC) that allow for precise adjustments in the bending process, improving accuracy and repeatability.
Advantages of Vertical Press Brakes
Vertical press brakes offer several key advantages that make them an appealing choice for specific metalworking needs:
- Space-Saving Design for Compact Workshops
One of the most notable benefits of vertical press brakes is their compact footprint. Unlike traditional horizontal press brakes that require a lot of floor space, vertical models take up less room, making them ideal for workshops with limited space. This space efficiency allows businesses to maximize their workshop layout without sacrificing the capabilities of their press brake machine. - Increased Precision for Small Parts and Intricate Bends
Vertical press brakes excel when it comes to handling smaller parts and producing complex, intricate bends. The vertical pressing action offers greater control and precision, allowing operators to achieve tighter tolerances and more accurate angles. This is especially important for industries such as aerospace, electronics, and custom prototyping, where detail and accuracy are critical. - Versatility for Different Types of Metalworking
Vertical press brakes are versatile machines capable of working with a wide range of materials, from soft metals like aluminum to high-strength materials like steel. They can accommodate various bending processes, including V-bending, air bending, and bottom bending, making them suitable for different types of metalworking projects. Whether producing prototypes, custom parts, or high-precision components, vertical press brakes provide flexibility in bending operations.
Common Applications of Vertical Press Brakes
Vertical press brakes are particularly valuable in industries where precision, space efficiency, and the ability to handle intricate bends are critical. Here are some of the industries and types of workpieces that commonly benefit from vertical press brakes:
- Aerospace
The aerospace industry demands extremely tight tolerances and high precision for components like brackets, panels, and small structural parts. Vertical press brakes, with their accurate bending capabilities, are ideal for producing these intricate components while ensuring consistency and meeting stringent quality standards. - Automotive
In the automotive sector, vertical press brakes are used to create complex metal parts, such as small brackets, connectors, and other custom components. The precision of vertical press brakes is essential for producing parts that fit perfectly in vehicle assemblies while maintaining the strength and integrity required in automotive manufacturing. - Prototyping and Custom Fabrication
Vertical press brakes are commonly used in prototyping and custom fabrication workshops where small-batch or one-off parts are created. Their versatility allows for bending different materials and creating unique shapes, making them perfect for custom projects requiring special attention to detail. - Electronics and Precision Equipment Manufacturing
Small and intricate metal parts used in electronics and precision equipment often require delicate bending operations. Vertical press brakes provide the necessary control and accuracy for creating these fine, detailed components without damaging the materials.
Specific Types of Workpieces and Materials
- Small Parts: Vertical press brakes are especially suited for bending smaller metal parts, such as brackets, connectors, and supports, where high precision is necessary.
- Sheet Metal: They handle a wide variety of materials, including aluminum, stainless steel, copper, and brass, offering versatility for different projects.
- Intricate Shapes: The ability to produce intricate bends with tight tolerances makes vertical press brakes an ideal tool for creating complex shapes and components required in advanced manufacturing.
Vertical vs. Horizontal Press Brakes
When selecting the right press brake for your workshop, understanding the differences between vertical and horizontal press brakes is essential. While both machines serve the same purpose—bending and shaping sheet metal—there are notable distinctions in design, functionality, and ideal applications.
In-Depth Comparison of Vertical and Horizontal Models
- Orientation and Space Usage
- Vertical Press Brakes: As the name suggests, vertical press brakes operate with a vertical pressing action, where the upper die moves downward to bend the material. This design is space-efficient, occupying less floor space, making it suitable for smaller workshops or production lines with limited room.
- Horizontal Press Brakes: These are more commonly used in large-scale operations. Horizontal models perform bending along a horizontal axis, which typically requires more floor space but allows for greater flexibility in handling larger workpieces.
- Precision and Application
- Vertical Press Brakes: Known for their precision, vertical press brakes excel at creating intricate bends and working with smaller or more delicate parts. They offer tight control over the bending process, making them ideal for industries like aerospace, electronics, and custom fabrication.
- Horizontal Press Brakes: Horizontal models are versatile and widely used in industries with high production volumes, such as automotive and heavy manufacturing. They are capable of handling larger sheets of metal and are often used for high-capacity bending with less focus on extreme precision.
- Production Capacity
- Vertical Press Brakes: These machines are typically used for low to medium production volumes or for creating custom, detailed parts. They may not handle high-volume production as efficiently as horizontal models.
- Horizontal Press Brakes: Designed for high-volume production, horizontal models are capable of faster cycle times and can handle large sheets of metal more efficiently, making them suitable for mass production environments.
- Cost and Maintenance
- Vertical Press Brakes: Vertical machines tend to be more affordable and require less maintenance, particularly in workshops focused on precision over sheer volume.
- Horizontal Press Brakes: While generally more expensive due to their size and capacity, horizontal press brakes are built for durability and high production output, which can justify the higher initial investment for larger-scale operations.
Scenarios Where a Vertical Press Brake Is More Advantageous
- Limited Workshop Space: If your workspace is small or crowded, a vertical press brake’s compact design can save significant floor space without sacrificing the ability to perform complex bending tasks.
- High-Precision Requirements: For industries that demand extreme accuracy, such as aerospace or electronics, vertical press brakes provide the tight tolerances needed for detailed and intricate bends.
- Custom or Low-Volume Production: Vertical press brakes are a great choice for custom fabrication or prototyping, where flexibility and precision are more important than high production volume. They allow operators to easily switch between different setups for varied, low-volume projects.
- Smaller Parts and Thin Materials: Vertical press brakes are well-suited for working with smaller parts or thin sheets of metal, where precise control and delicate handling are required to prevent damage or deformation.
In summary, vertical press brakes are ideal for precision work, smaller spaces, and detailed bending tasks, while horizontal press brakes are better suited for large-scale, high-volume production where flexibility and speed are paramount.