Fiber Laser cutting Machine is often considered one of the best methods for sheet metal fabrication due to several key advantages:
1.Precision: Laser cutting offers exceptional precision, allowing for intricate designs and tight tolerances. The focused laser beam can cut through the metal with high accuracy, resulting in clean edges and minimal material wastage.
2.Versatility: Laser cutting can be used on a wide range of materials, including various types of metals, such as steel, aluminum, brass, and copper. It can also handle different thicknesses of sheet metal, making it a versatile option for various applications.
3.Speed: Laser cutting is typically faster than traditional methods such as manual cutting or mechanical cutting processes. The laser beam can move quickly across the sheet metal, leading to shorter production times and increased efficiency.
4.lexibility: Laser cutting machines can be programmed to cut complex shapes and patterns, making it suitable for both prototyping and production runs. This flexibility allows manufacturers to adapt quickly to changing design requirements and produce customized parts with ease.
5.Minimal Heat Affected Zone (HAZ): Laser cutting produces a small heat-affected zone compared to other cutting methods, reducing the risk of distortion or warping in the metal. This is particularly important for delicate materials or components that require precise dimensions.
6.Automation and Integration: Laser cutting can be easily integrated into automated production lines, allowing for high-volume manufacturing with minimal human intervention. This automation helps to streamline the fabrication process and improve overall productivity.
7.Cost-effectiveness: While the initial investment in laser cutting equipment may be higher than some other methods, the long-term cost savings can be significant. With its speed, precision, and versatility, laser cutting can reduce labor costs, minimize material waste, and optimize production efficiency, leading to overall cost savings for manufacturers.
Overall, laser cutting offers numerous advantages that make it an ideal choice for sheet metal fabrication, particularly when precision, speed, versatility, and cost-effectiveness are essential considerations.
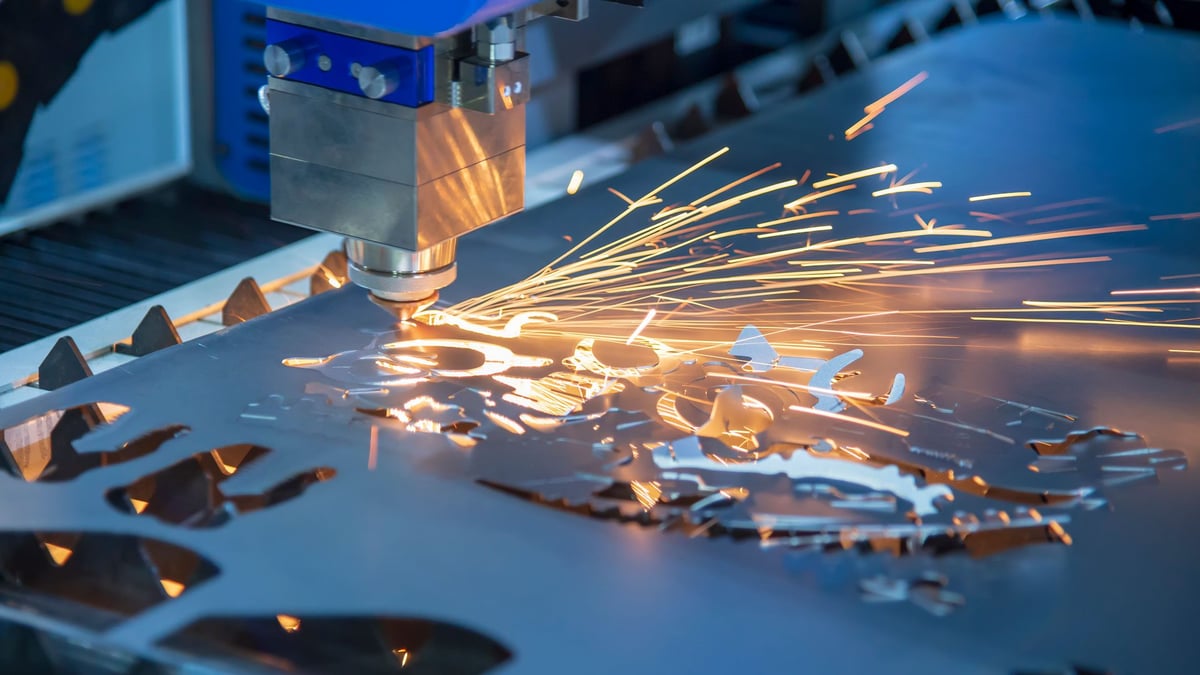
Types of Laser Cutters and How They Work
- CO2 laser cutters are the most common type used for sheet metal fabrication, woodworking, and other materials.
- They use a carbon dioxide gas mixture as the laser medium to produce the laser beam.
- The cutting head focuses the laser beam onto the material, causing it to vaporize or melt, which results in cutting through the material.
- CO2 laser cutters are versatile and can cut through a wide range of materials, including metals, plastics, wood, fabric, and more.
- The laser beam is generated in a resonator and directed through a series of mirrors to the cutting head.
- There are several types of laser cutters, each utilizing different types of lasers and mechanisms for cutting materials. Here are some common types and how they work:
2.Fiber Laser Cutters:
- Fiber laser cutters utilize a solid-state laser source, typically a fiber laser, to generate the laser beam.
- The laser beam is transmitted through a flexible fiber optic cable to the cutting head.
- Fiber laser cutters are known for their high efficiency, speed, and precision, making them ideal for cutting thin to medium-thickness metals such as stainless steel, aluminum, and brass.
- They are commonly used in industrial applications such as automotive, aerospace, and electronics manufacturing.
3.Nd:YAG Laser Cutters:
- Nd:YAG (neodymium-doped yttrium aluminum garnet) laser cutters use a solid-state laser medium, typically Nd:YAG crystal, to produce the laser beam.
- The laser beam is generated in the laser medium and then directed to the cutting head through mirrors or fiber optics.
- Nd:YAG laser cutters are capable of cutting thick metals, ceramics, and other materials with high precision.
- They are commonly used in applications requiring deep penetration cutting or when high power density is needed.
Regardless of the type, the basic principle of laser cutting involves focusing a high-energy laser beam onto the surface of the material, which heats, melts, or vaporizes it to create the desired cut. The movement of the cutting head and the intensity of the laser beam are controlled by computer numerical control (CNC) systems, allowing for precise and accurate cutting of complex shapes and patterns.
Safey Precautions
Safety precautions are crucial when operating a fiber laser cutting machine due to the high-power laser beam and potential hazards associated with the cutting process. Here are some essential safety precautions to follow:
1.Protective Gear:
- Wear appropriate personal protective equipment (PPE) such as safety glasses with side shields to protect against laser radiation and flying debris.
- Use gloves when handling materials to prevent cuts and burns.
2.Machine Safety Features:
- Ensure that the machine is equipped with safety features such as emergency stop buttons, interlocks, and guarding to prevent access to the laser beam during operation.
- Familiarize yourself with the location and operation of emergency stops in case of an accident or malfunction.
3.Training and Certification:
- Ensure that operators receive comprehensive training on the safe operation of the fiber laser cutting machine.
- Only trained and authorized personnel should operate the equipment.
- Obtain any necessary certifications or licenses required for operating laser cutting machinery.
4.Material Handling:
- Handle materials with care and follow proper loading and unloading procedures to prevent accidents and injuries.
- Use lifting equipment or assistance for heavy or awkwardly shaped materials.
- Keep the work area clear of clutter to prevent tripping hazards.
5.Ventilation and Fume Extraction:
- Ensure adequate ventilation in the workspace to remove fumes, smoke, and airborne contaminants generated during the cutting process.
- Use a fume extraction system to capture and remove hazardous fumes from the cutting area.
- Follow manufacturer recommendations for ventilation requirements and maintenance of the extraction system.
6.Fire Prevention:
- Keep flammable materials away from the cutting area and ensure that combustible materials are properly secured.
- Have fire extinguishing equipment readily available and ensure that operators are trained in its use.
- Regularly inspect the machine and surrounding area for potential fire hazards.
7.Maintenance and Inspections:
- Perform regular maintenance and inspections of the fiber laser cutting machine according to the manufacturer's recommendations.
- Check for signs of wear, damage, or misalignment that could compromise safety or performance.
- Promptly repair or replace any faulty components to prevent accidents or malfunctions.
- By following these safety precautions and guidelines, operators can minimize the risk of accidents, injuries, and damage when operating a fiber laser cutting machine. Regular training, proper maintenance, and adherence to safety protocols are essential for ensuring a safe working environment.